Accessories for power supply series
Individual designs
Our company engage in on and comprehensively implements individual designs of metal enclosures and power supply units according to the needs, specifications and designs submitted by our clients. The purpose for carrying out individual designs is to ensure client’s maximum satisfaction. Therefore, the rule we have approved as the basis of our activity is to meet our clients’ requirements so that they are fully satisfied with the product and contact with our company. As far as individual products are concerned, we are able to use various types of solutions.
Production capabilities - 360° visualization
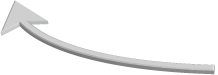
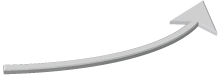
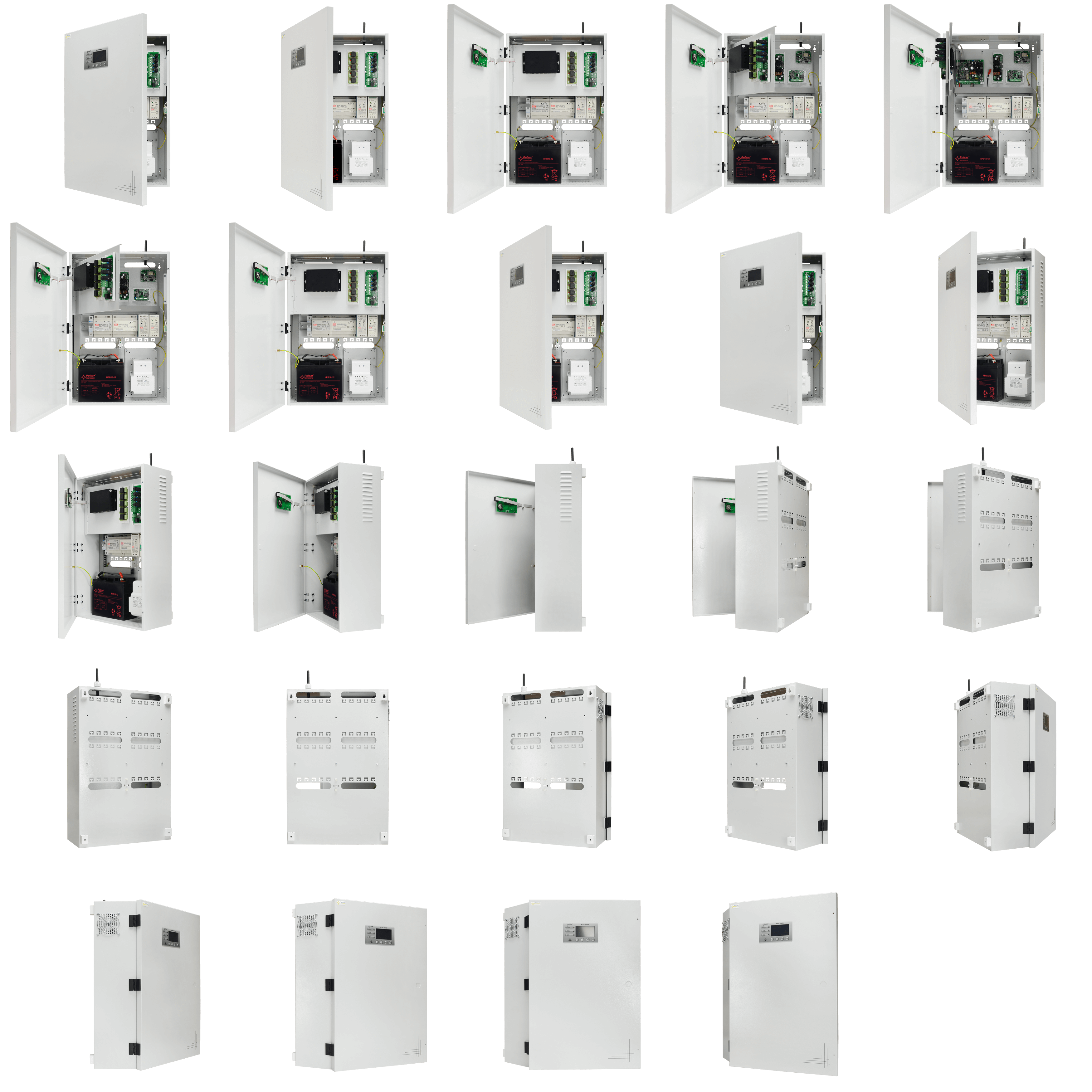
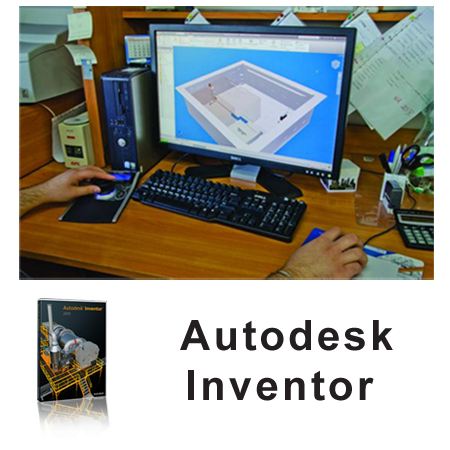
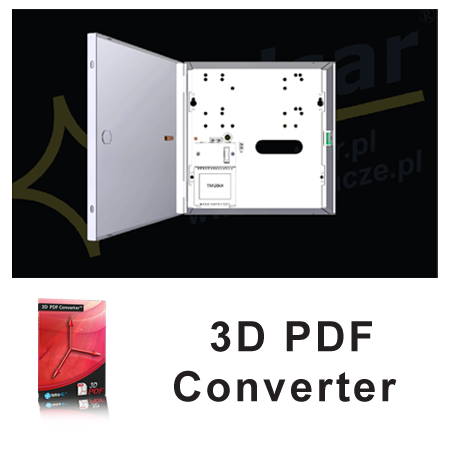
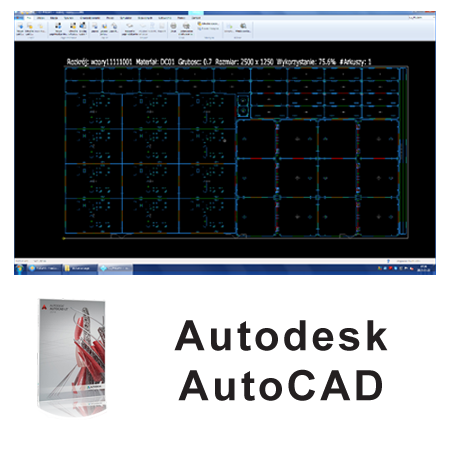
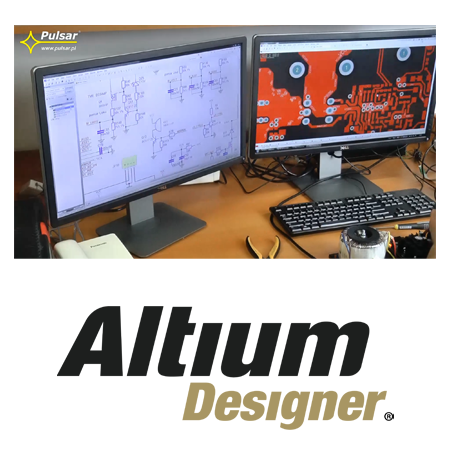
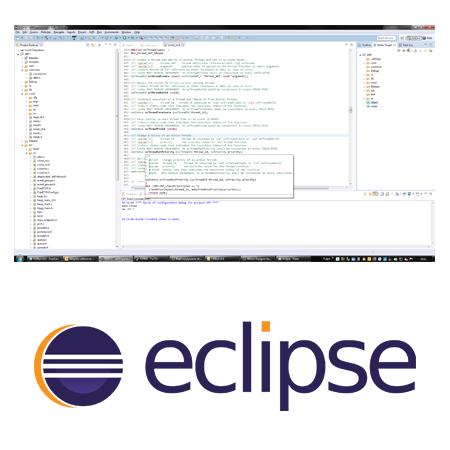
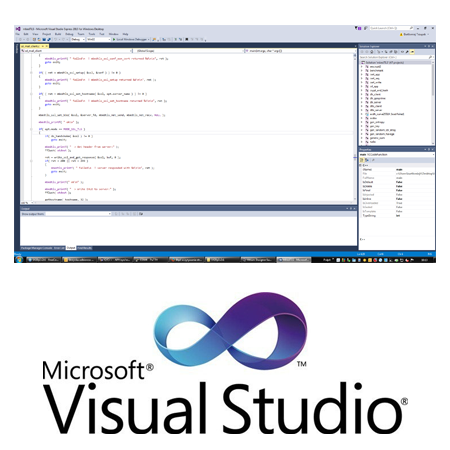
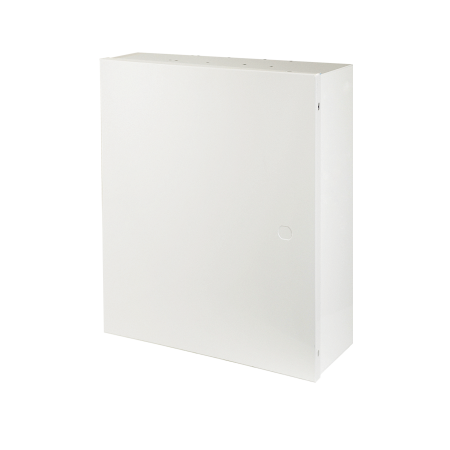
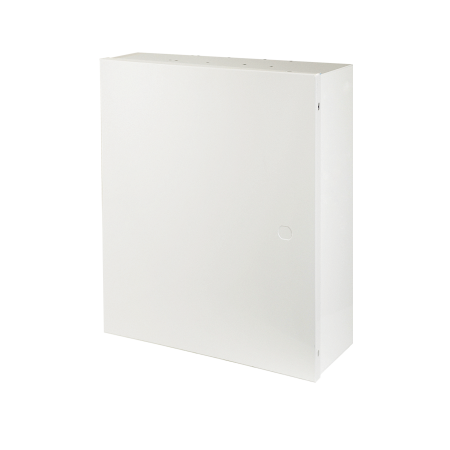
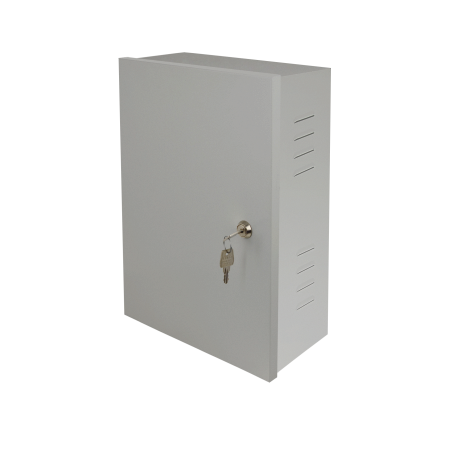
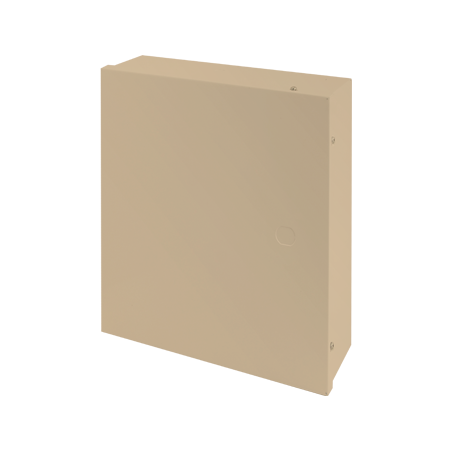
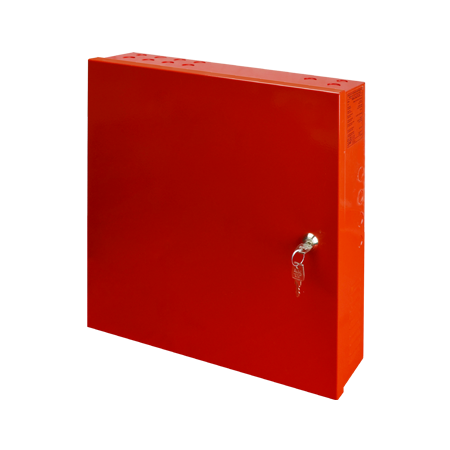
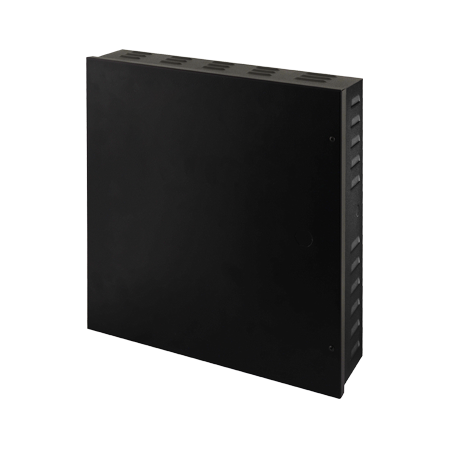
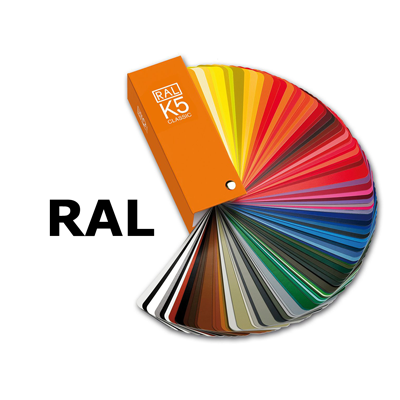
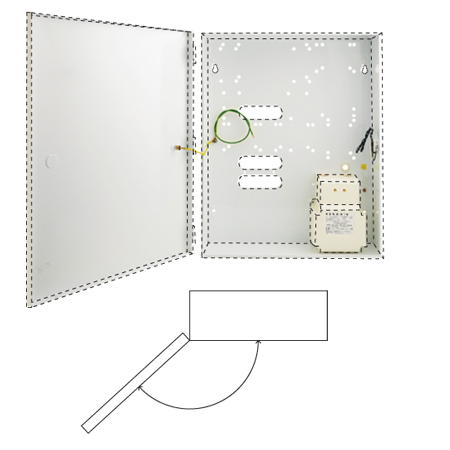
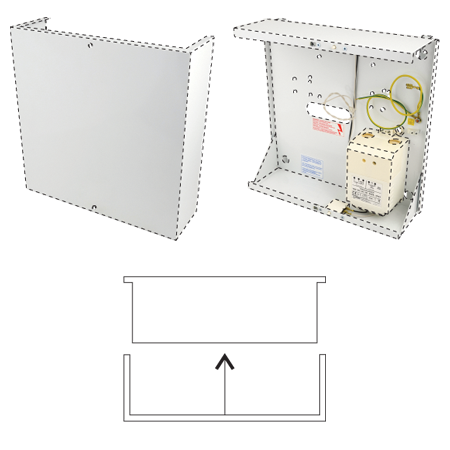
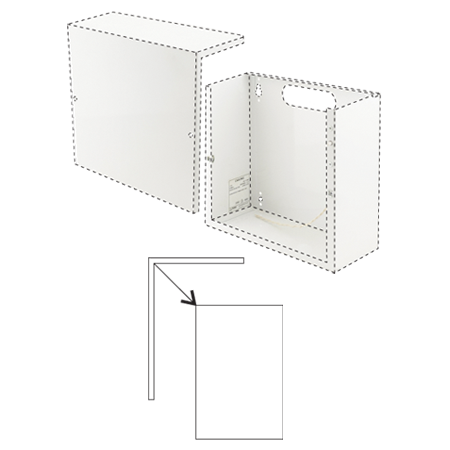
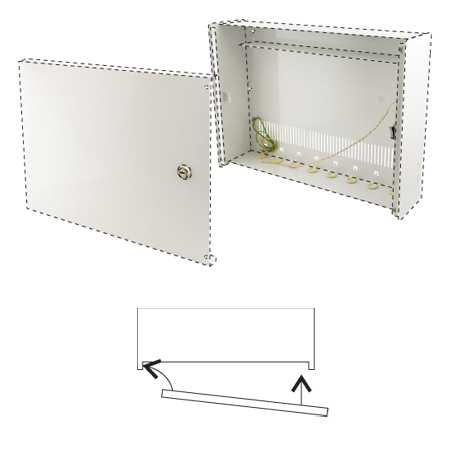
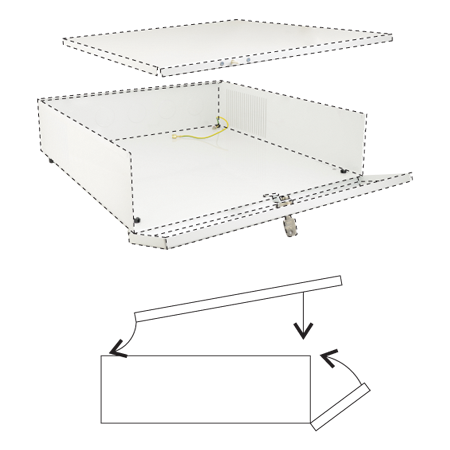
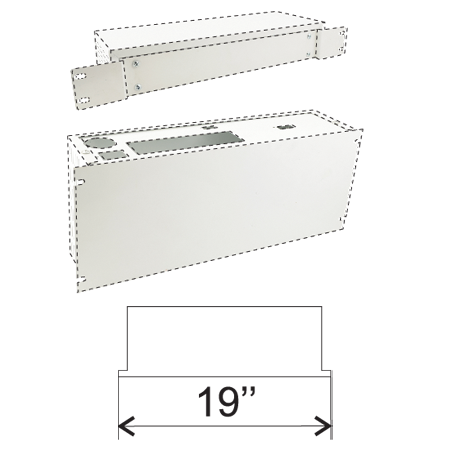
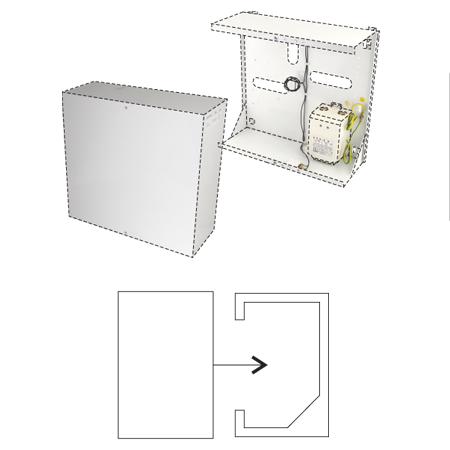
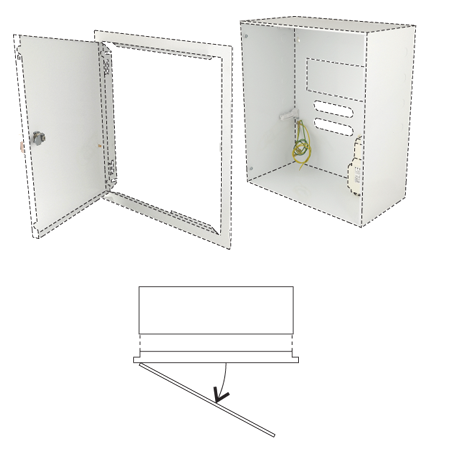
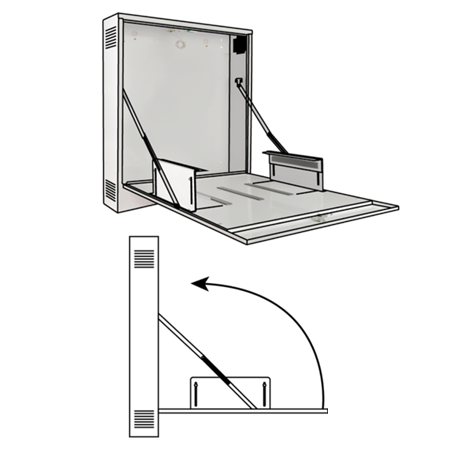
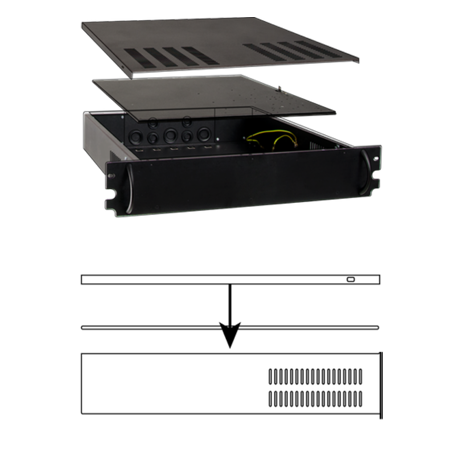
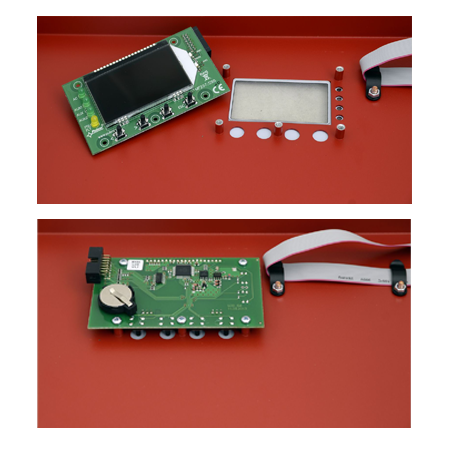
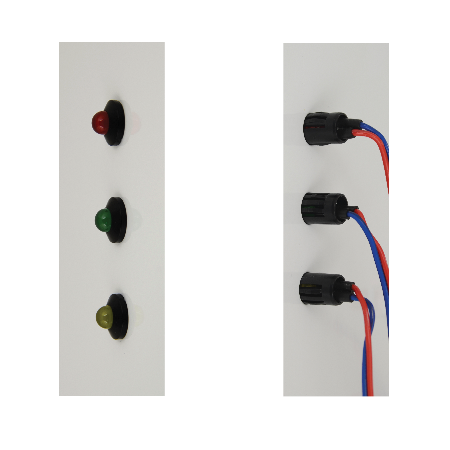
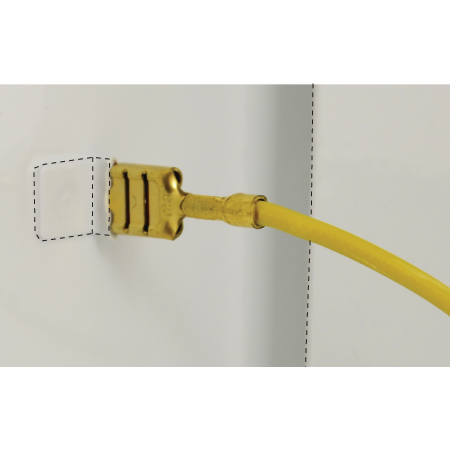
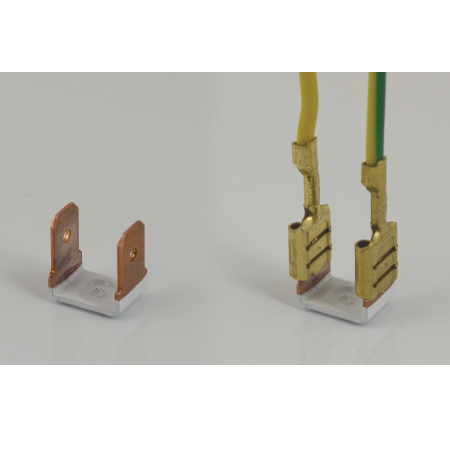
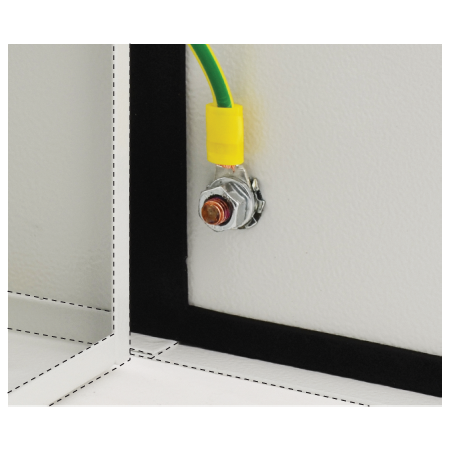
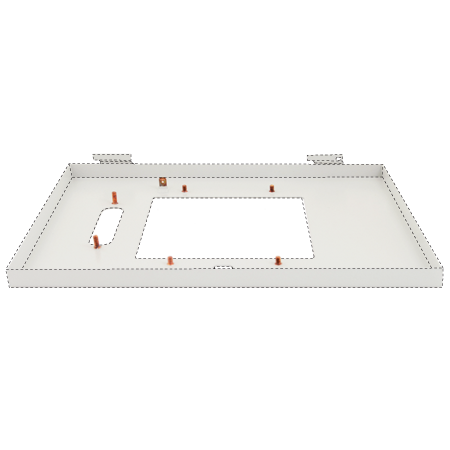
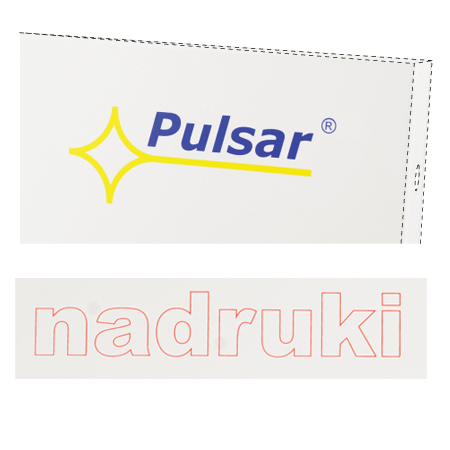
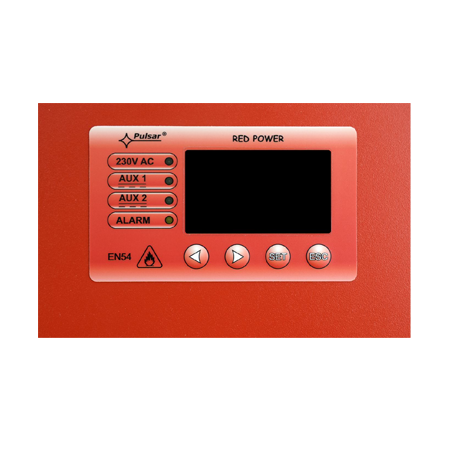
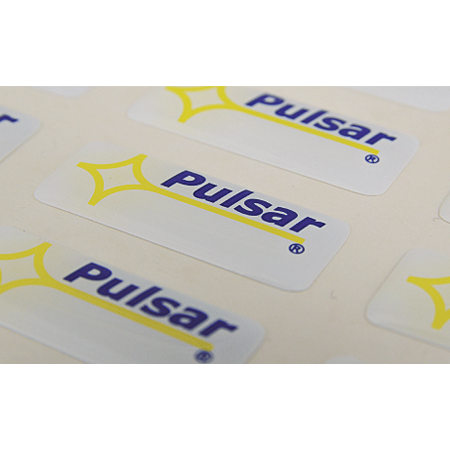
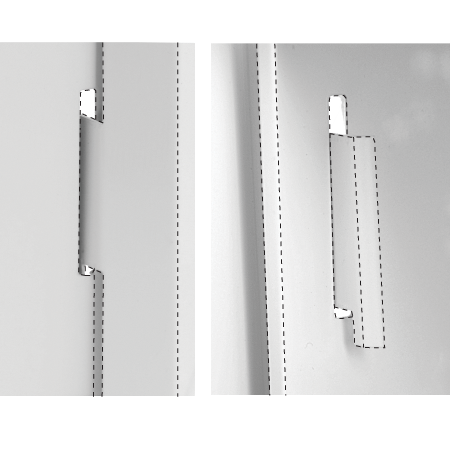
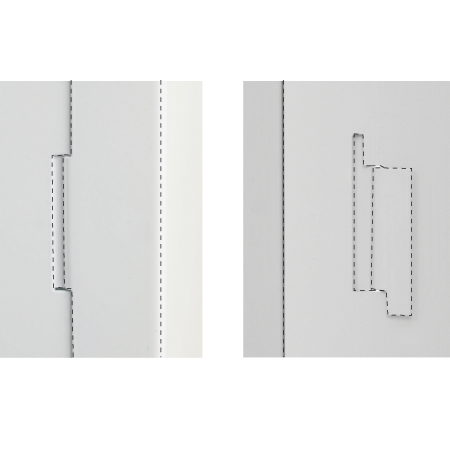
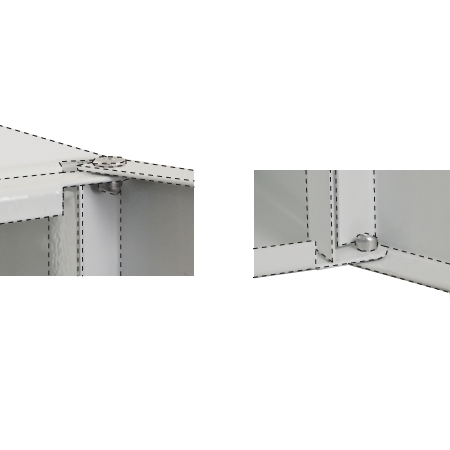
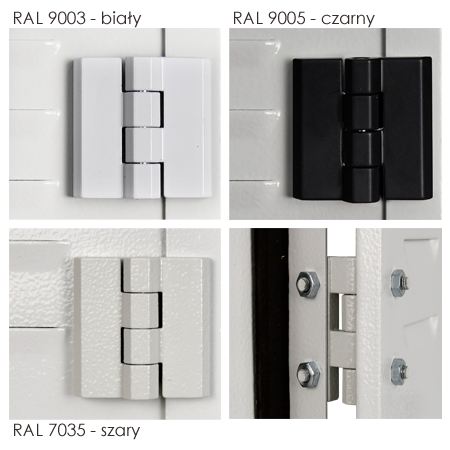
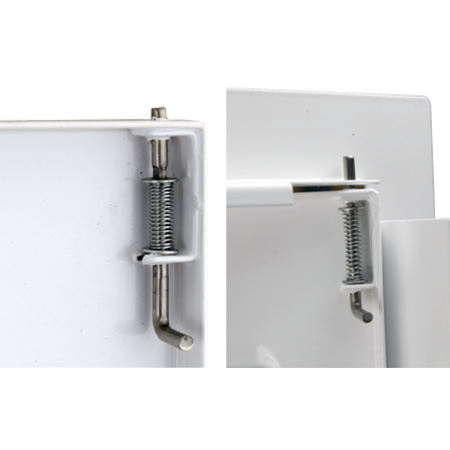
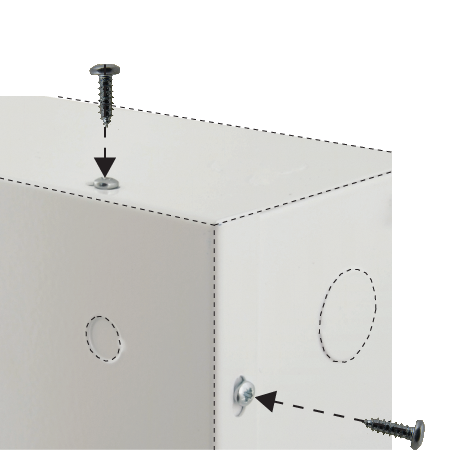
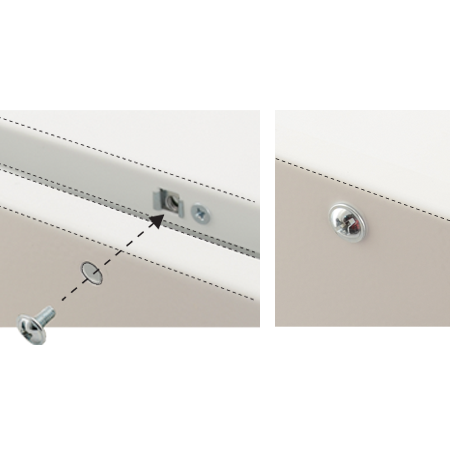
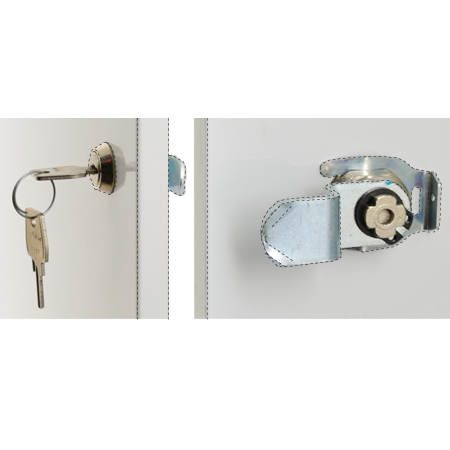
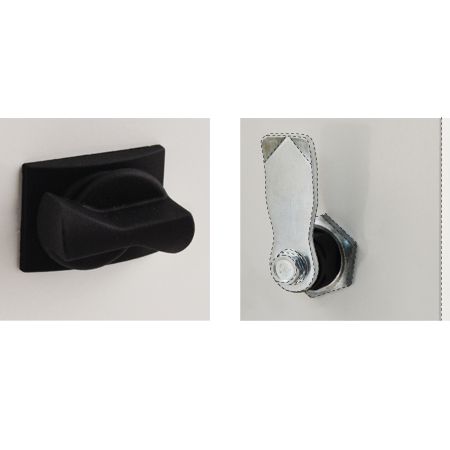
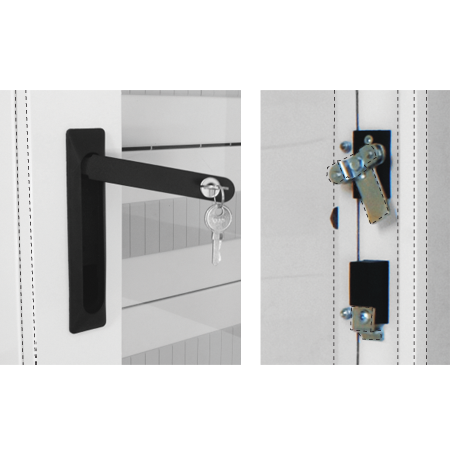
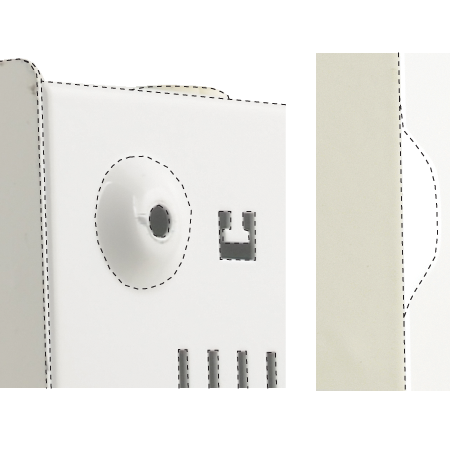
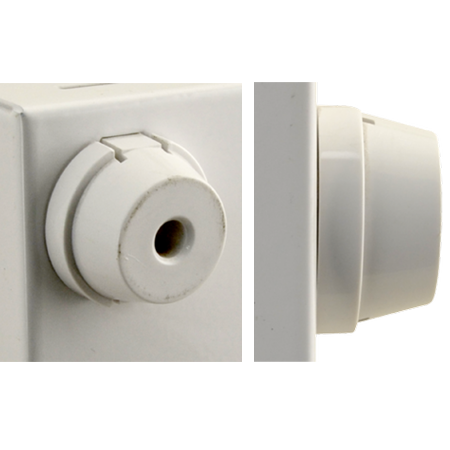
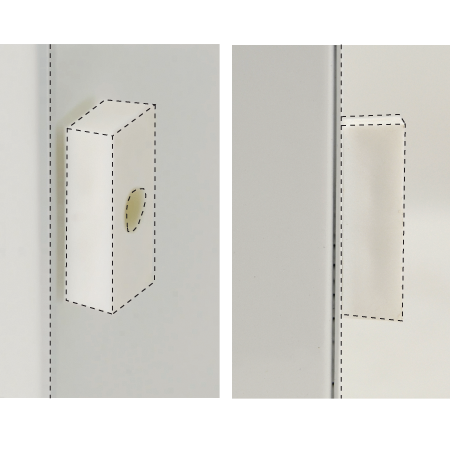
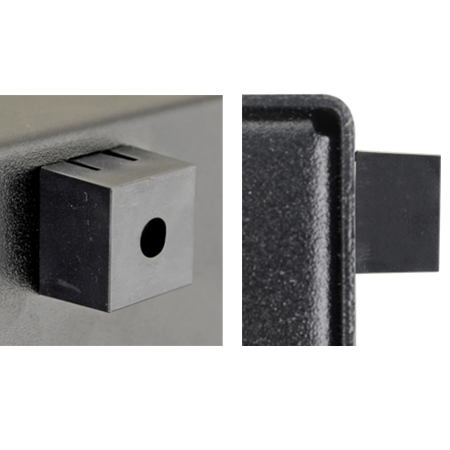
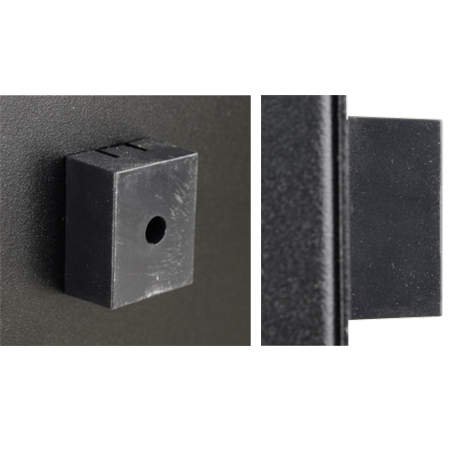
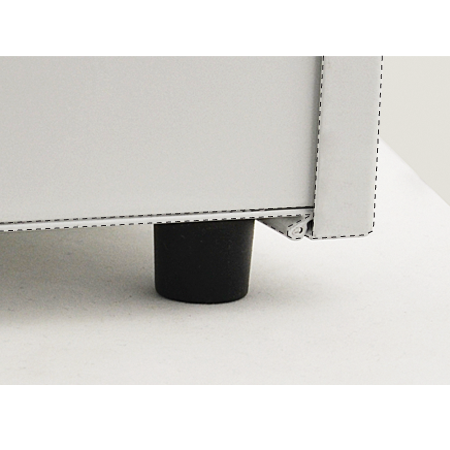
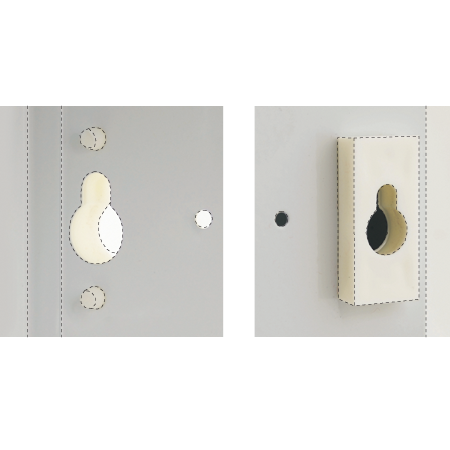
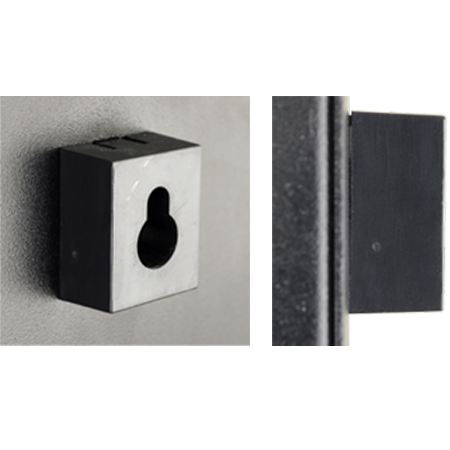
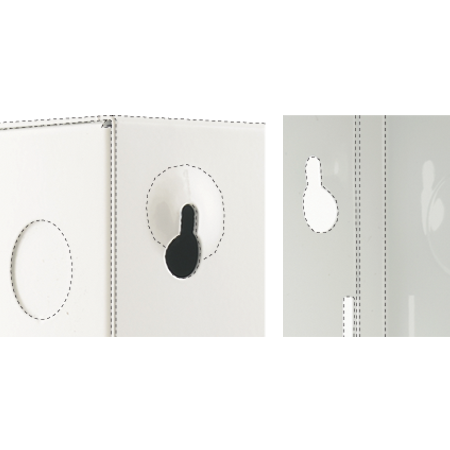
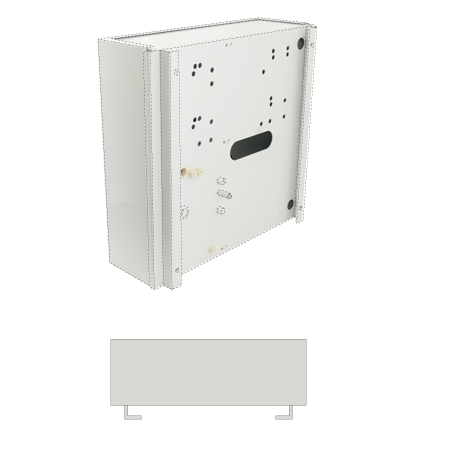
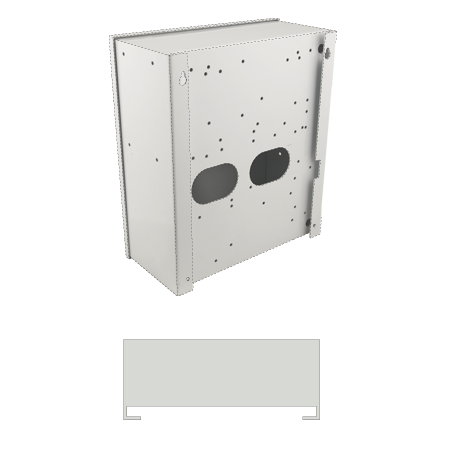
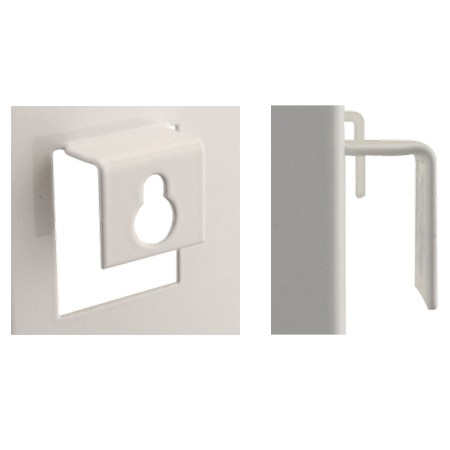
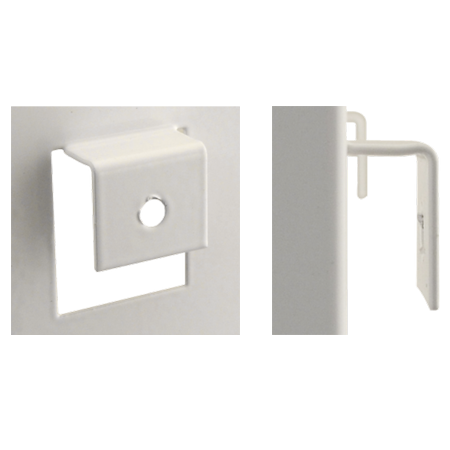
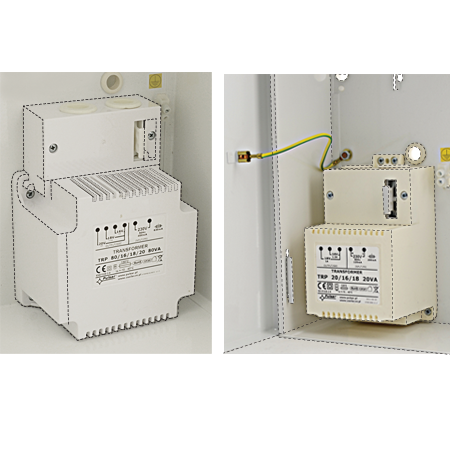
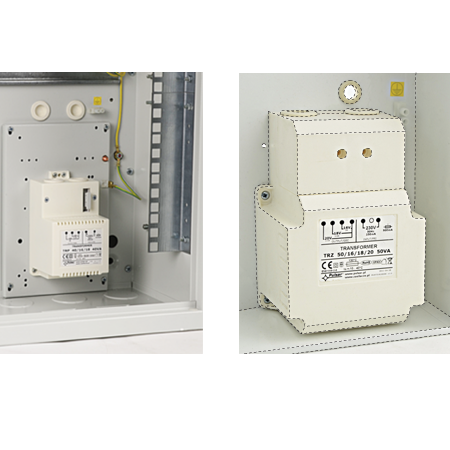
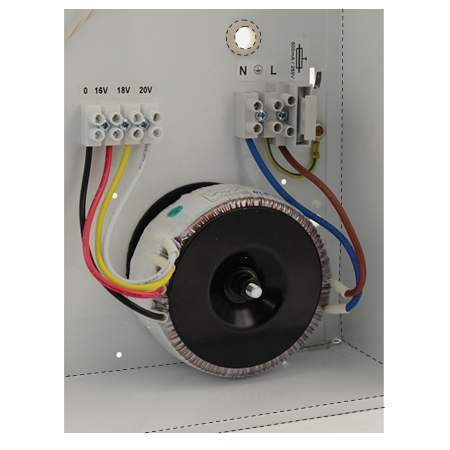
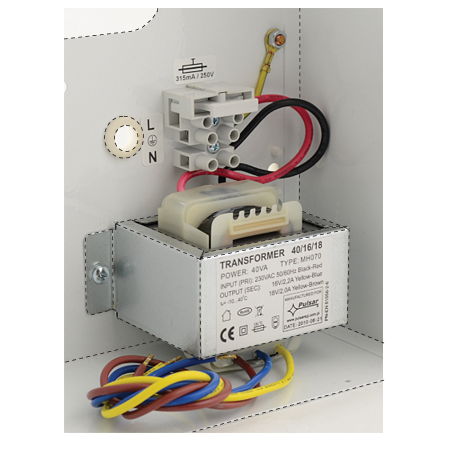
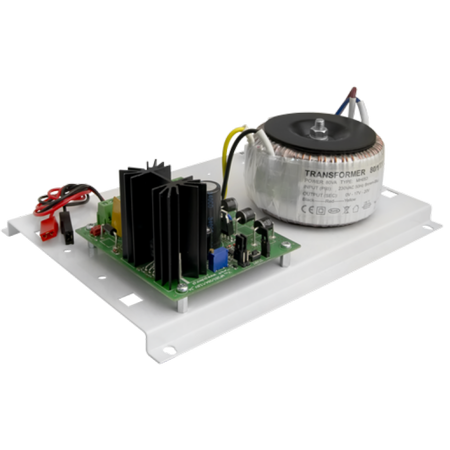
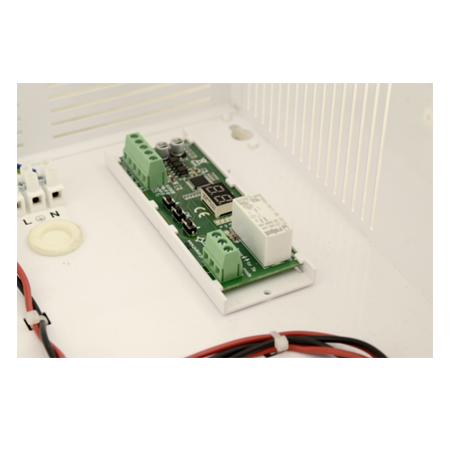
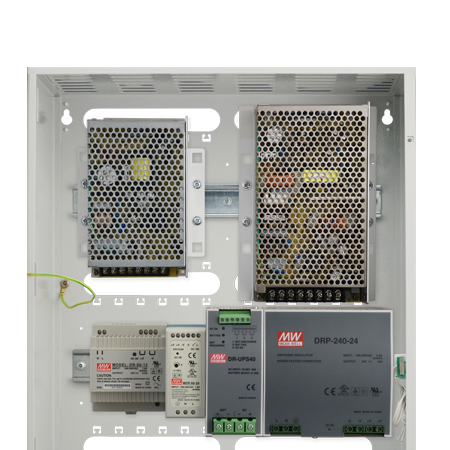
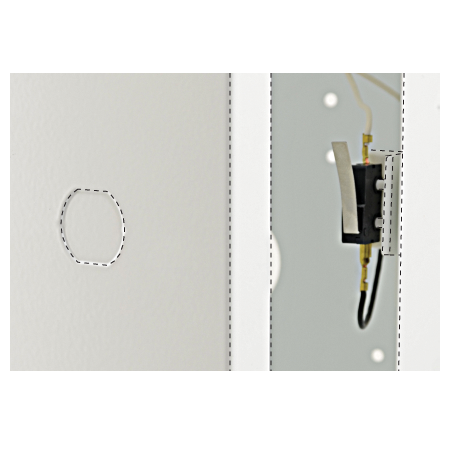
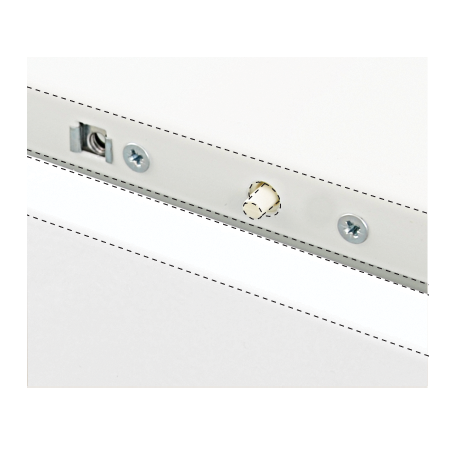
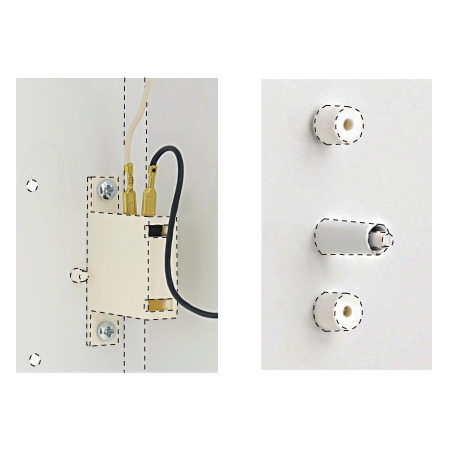
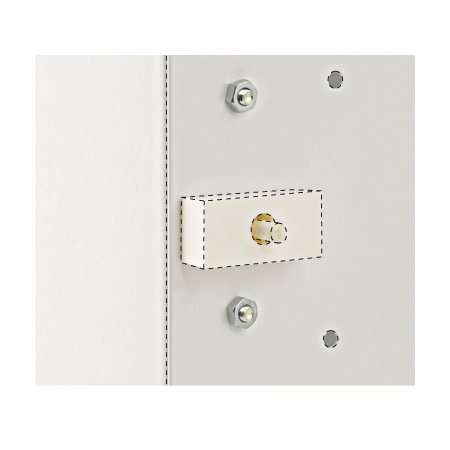
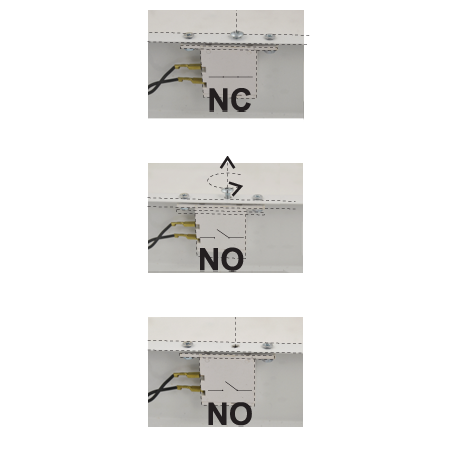
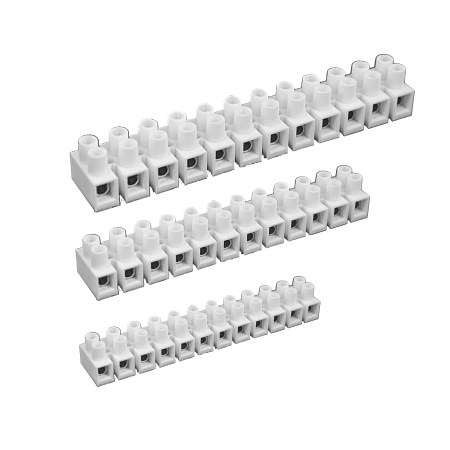
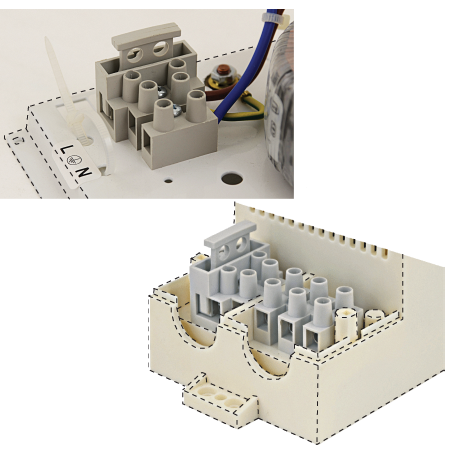
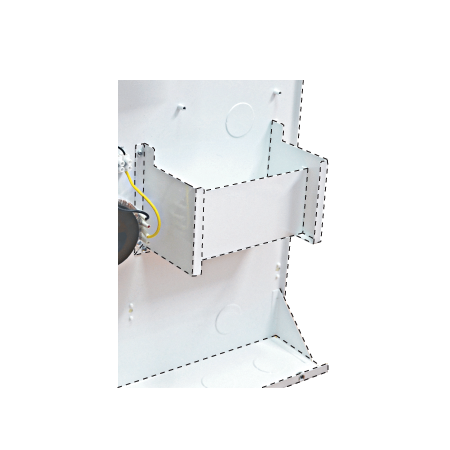
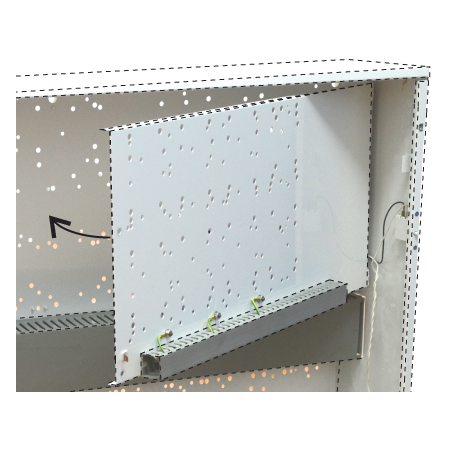


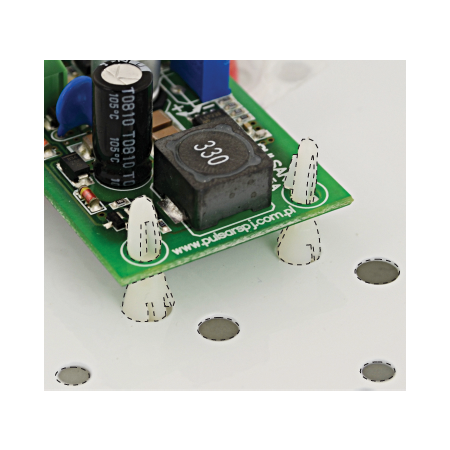
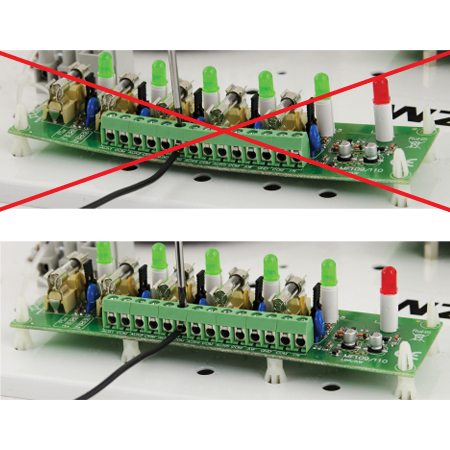
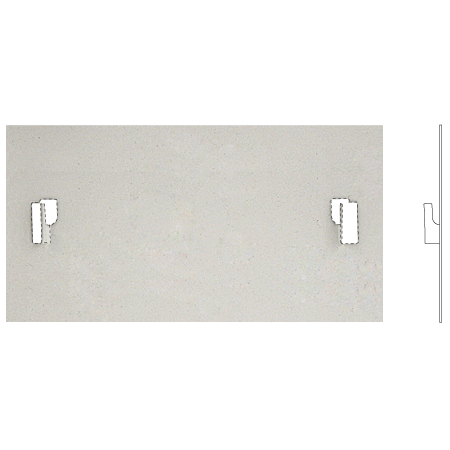
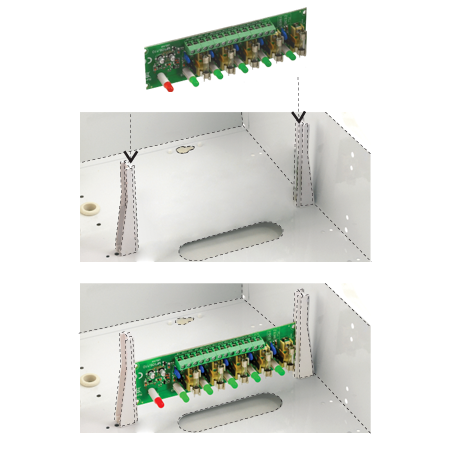

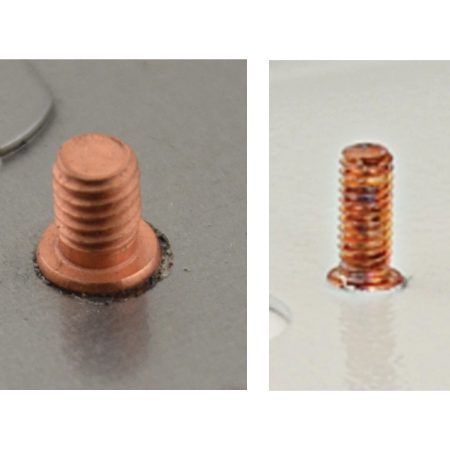
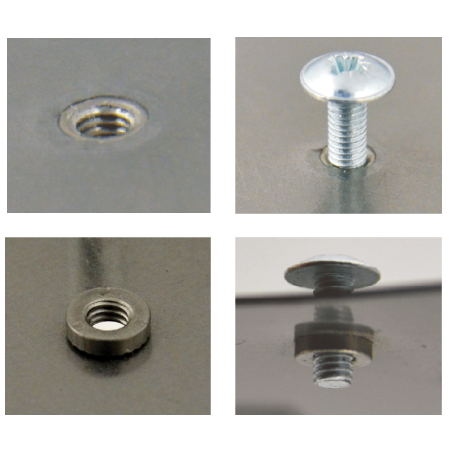
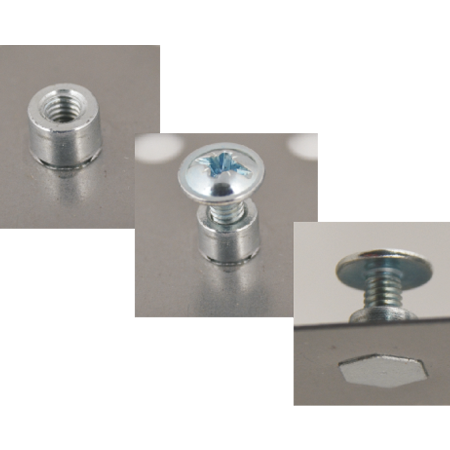
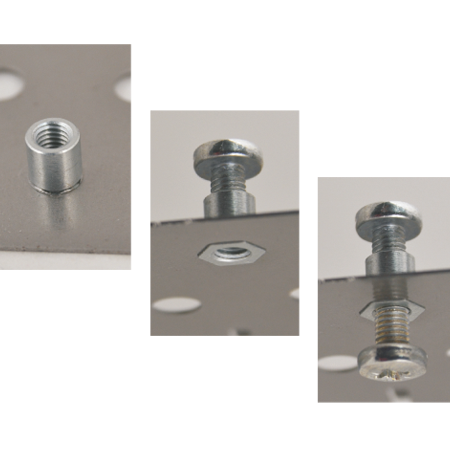
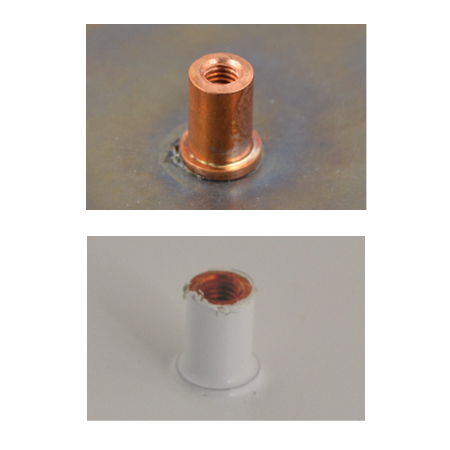
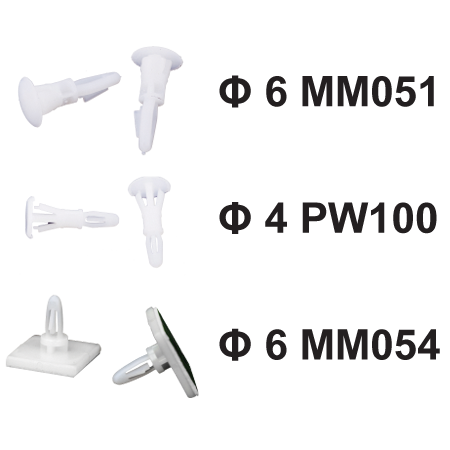
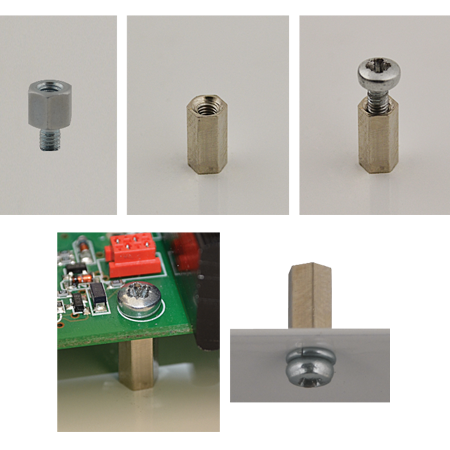
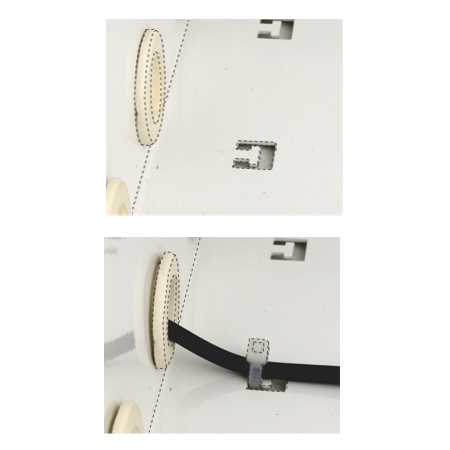
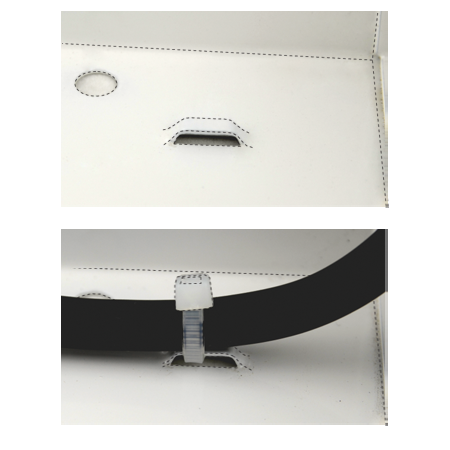
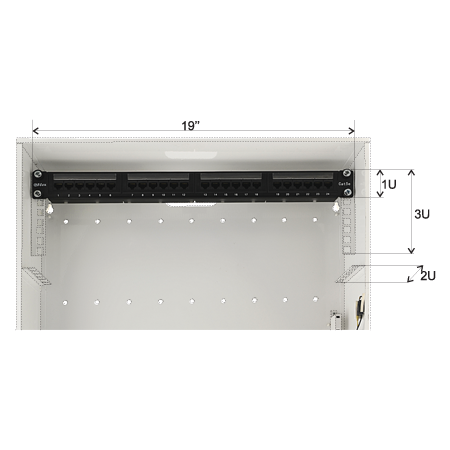
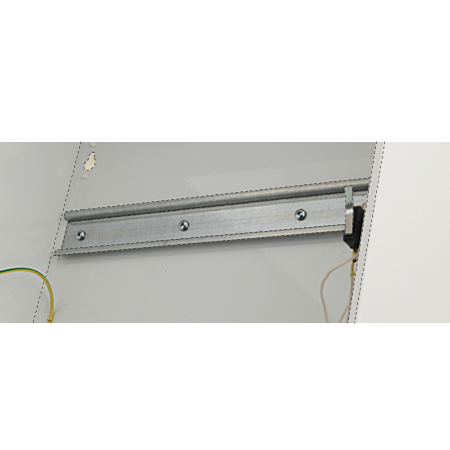
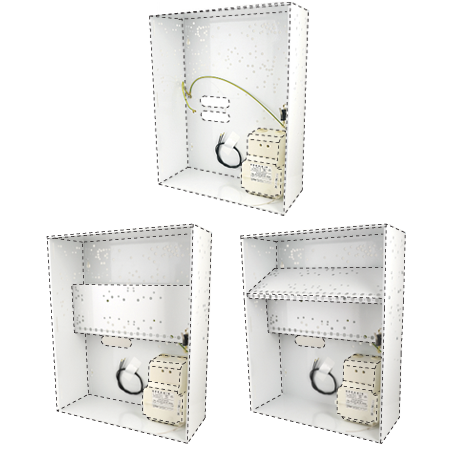
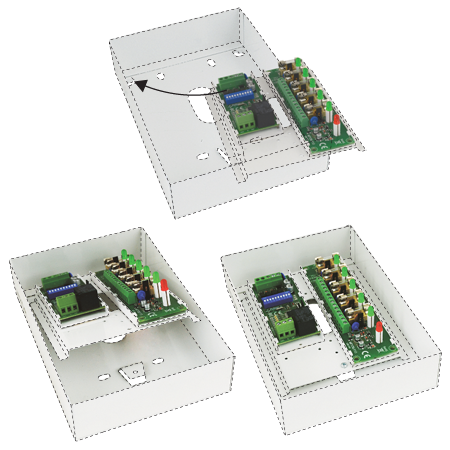
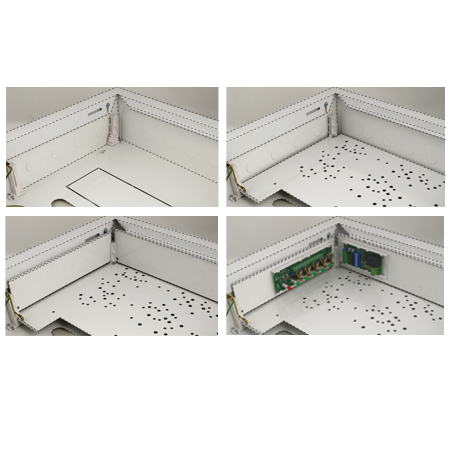
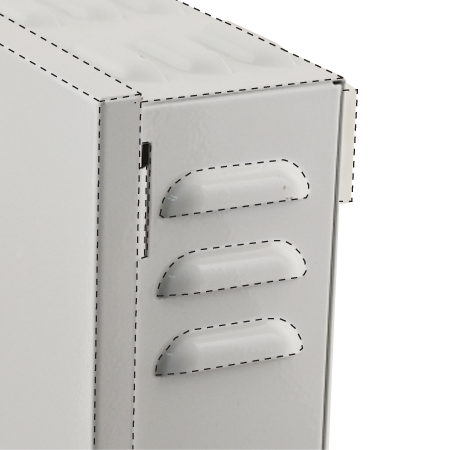
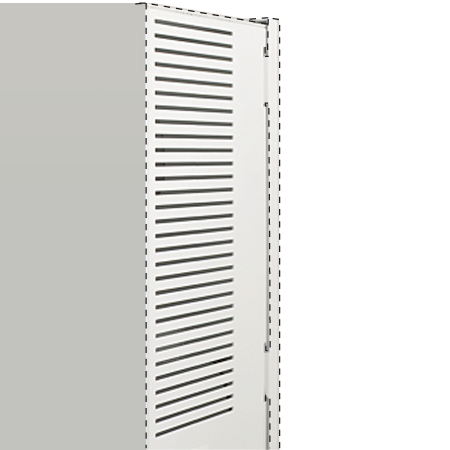
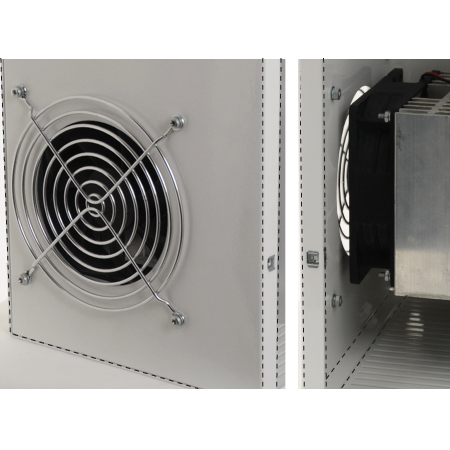
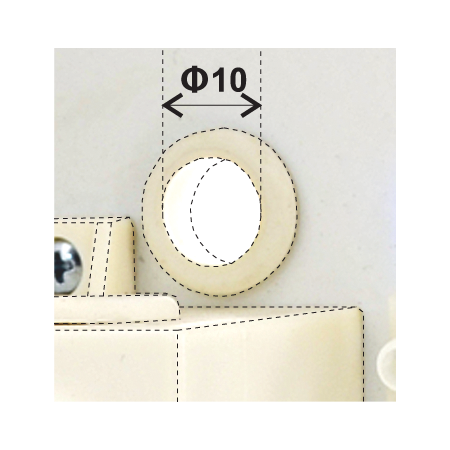
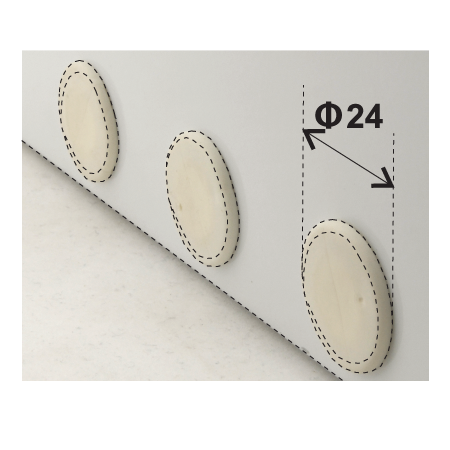
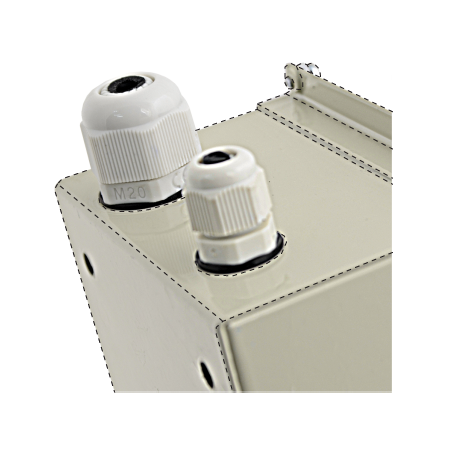
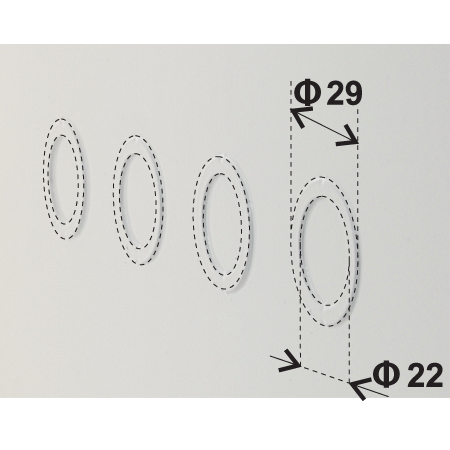
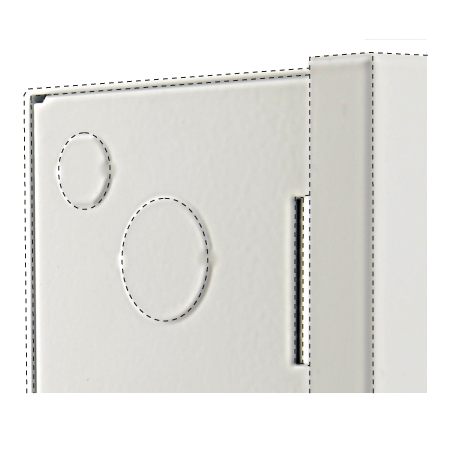
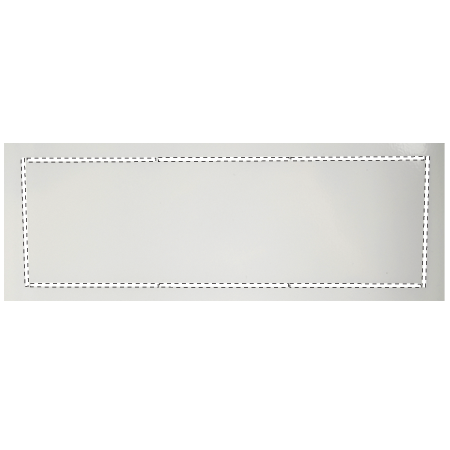
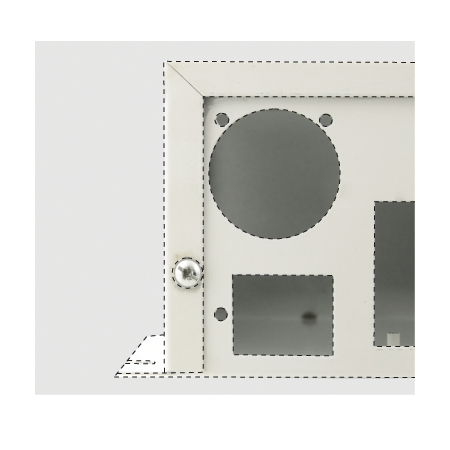
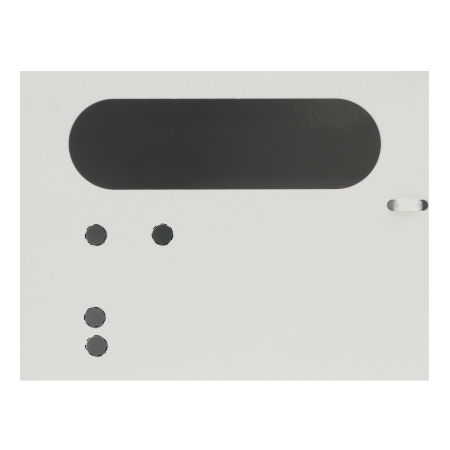

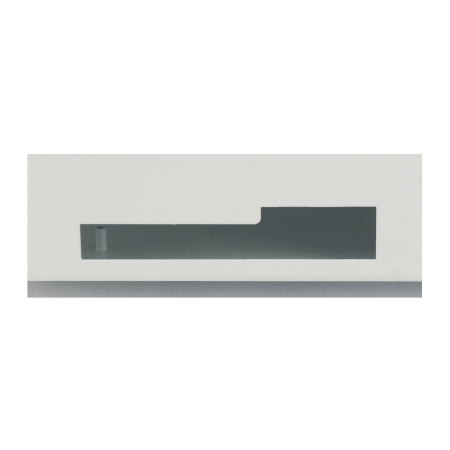
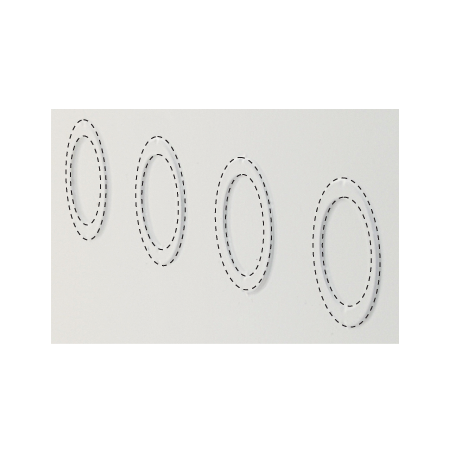
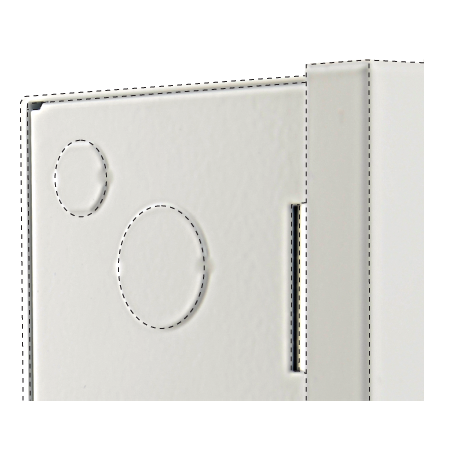
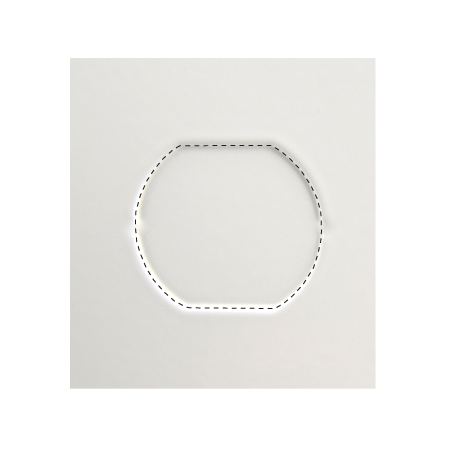
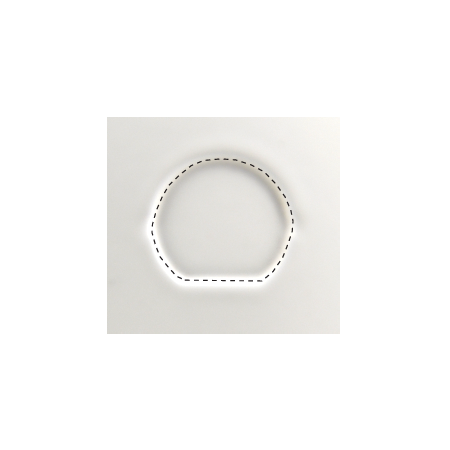
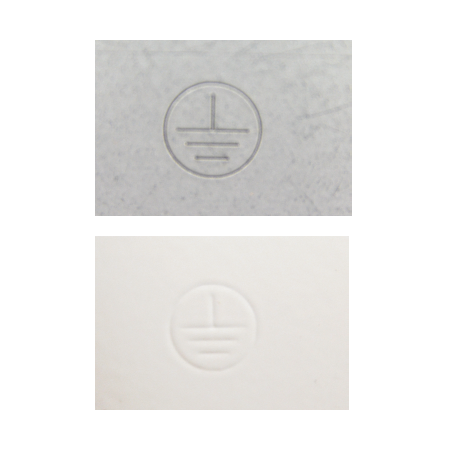
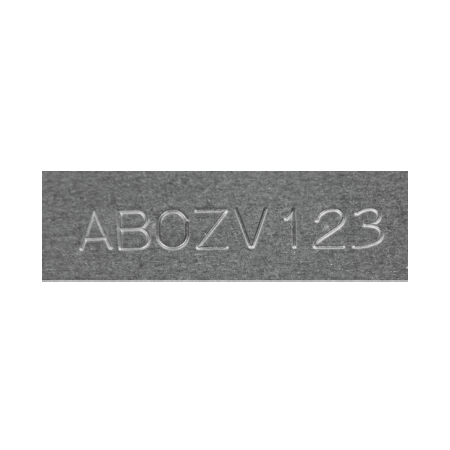
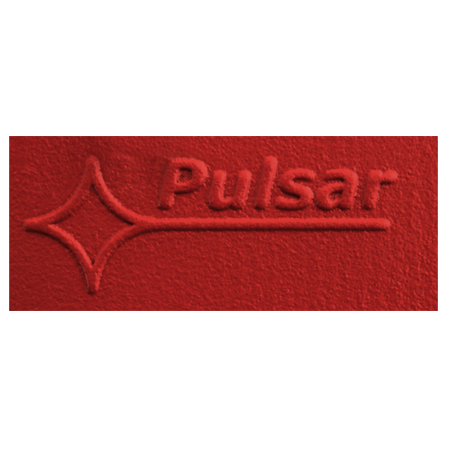
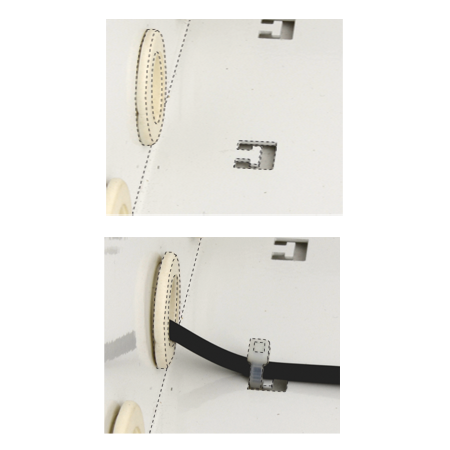
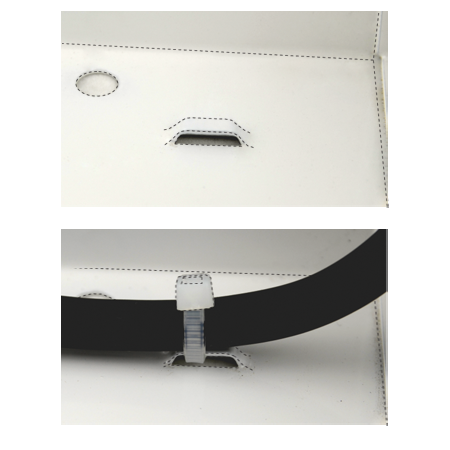
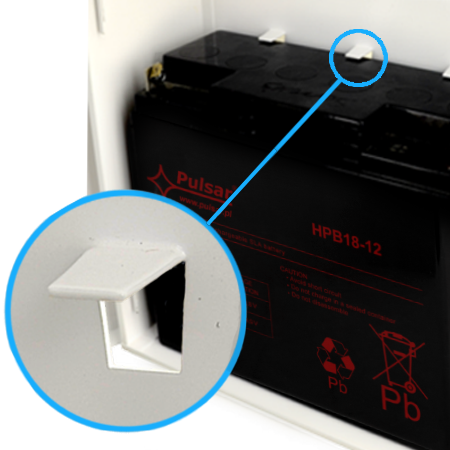
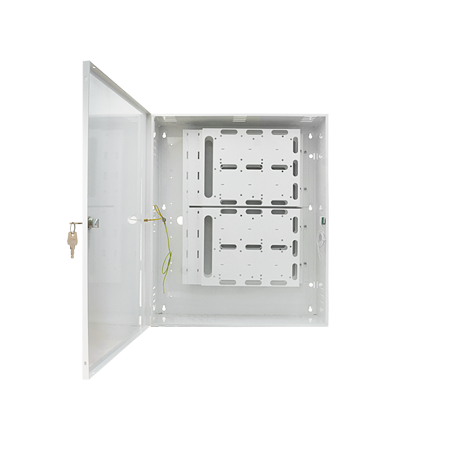
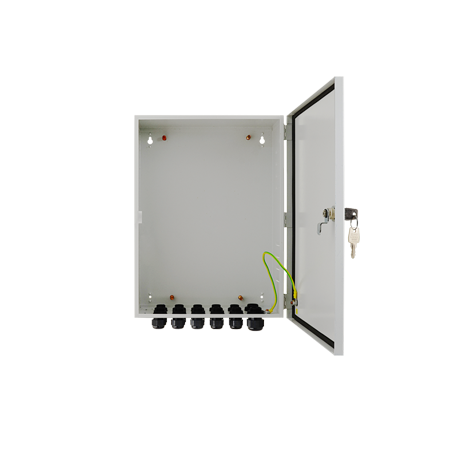
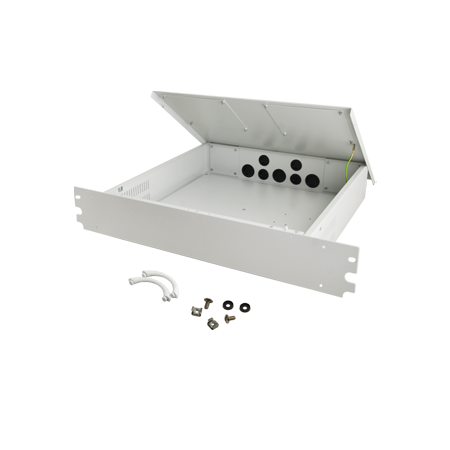

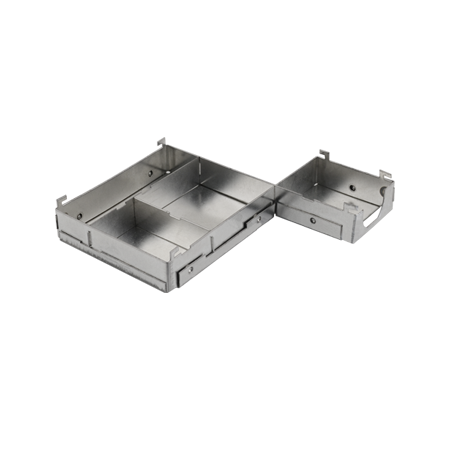
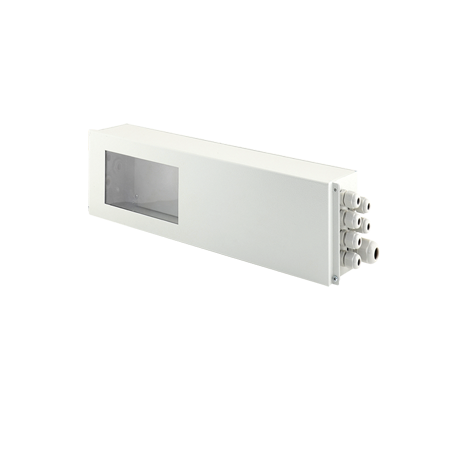

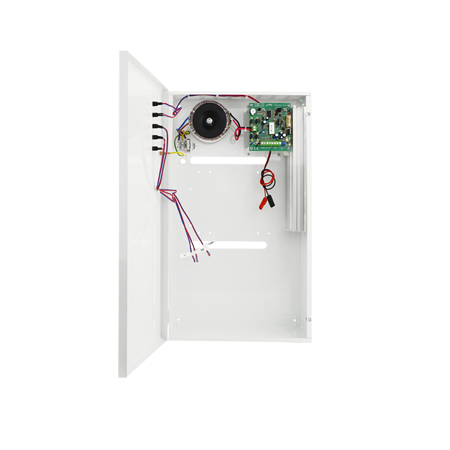
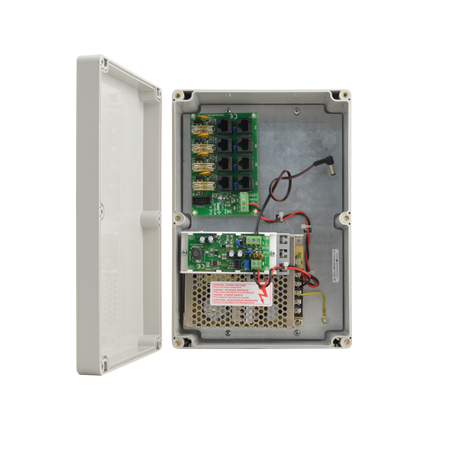
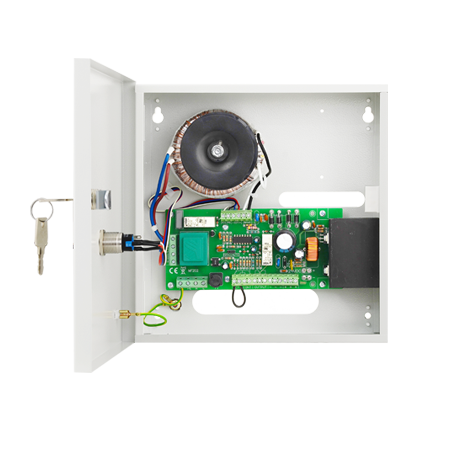
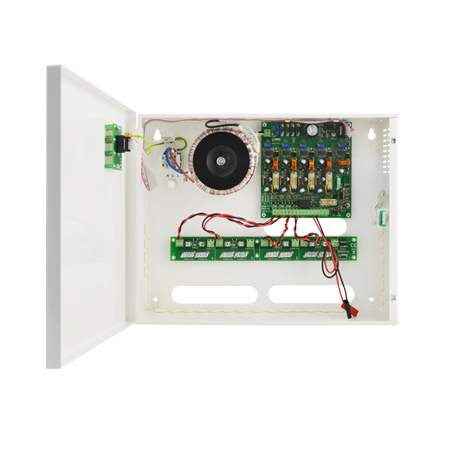
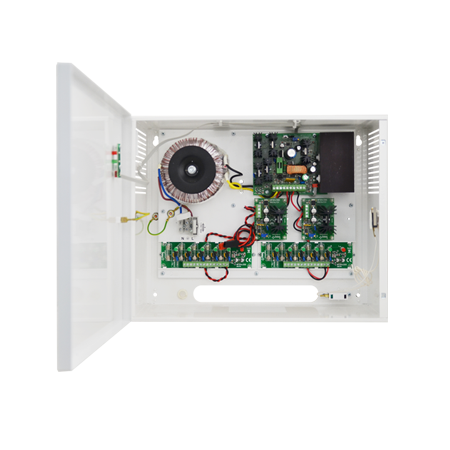
Designing enclosures
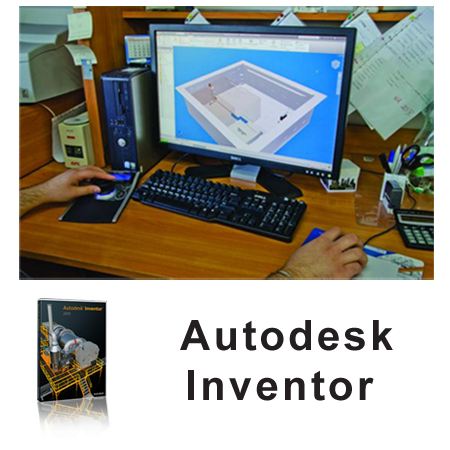
Autodesk Inventor
3D design
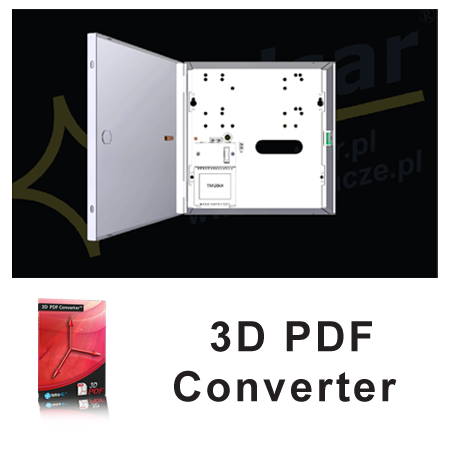
3D PDF Converter
Possibility to view project in 3D PDF
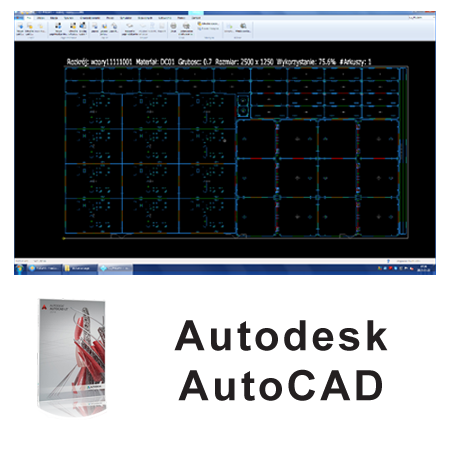
Autodesk AutoCAD
2D design
preparation for punching machine
designing power supplies - hardware / software
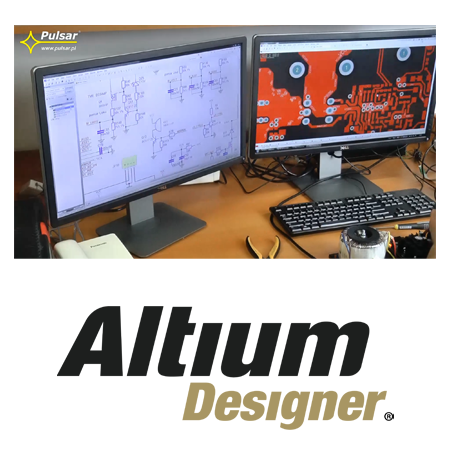
Altium Designer
hardware design
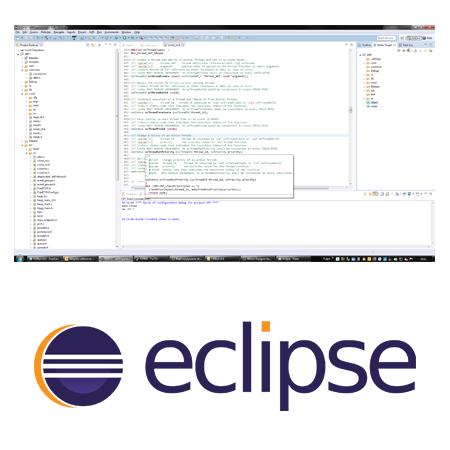
Eclipse
software design
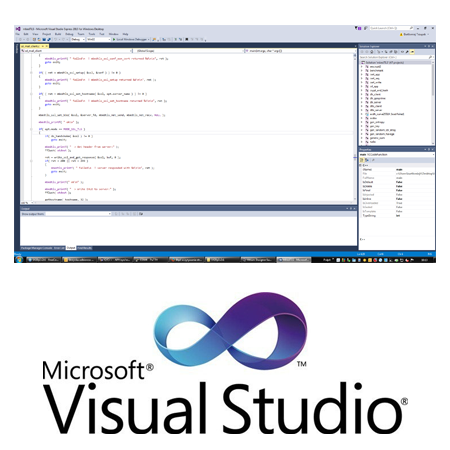
Microsoft Visual Studio
software design
Cutting
We owe a complex machinery stock, with digital-control cutting machines which can cut sophisticated designs from different types of sheet – depending on client’s preferences. Examples of metal sheets:
steel sheet - 0,7mm ÷ 1,5mm
galvanized sheet - 0,7mm ÷ 1,5mm
aluminium sheet - 1mm ÷ 1,5mm
tinned sheet - 0,5mm (for screens)
Colour
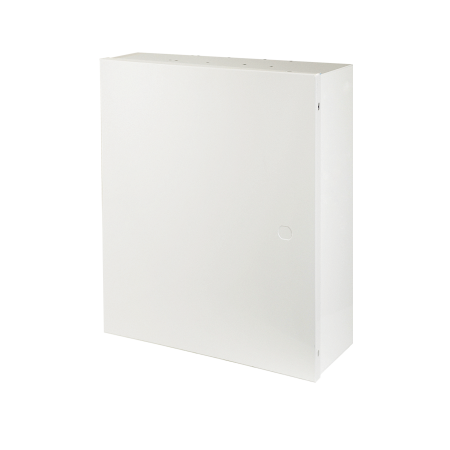
white RAL9003
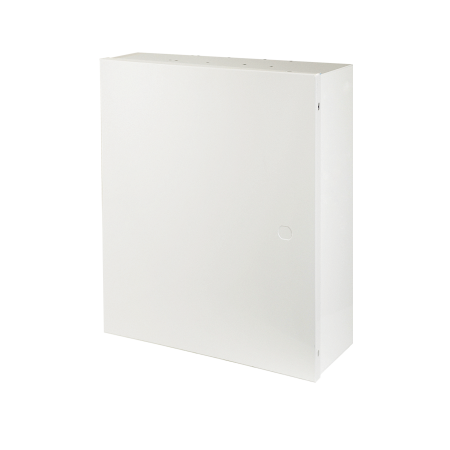
white - structure RAL 9003
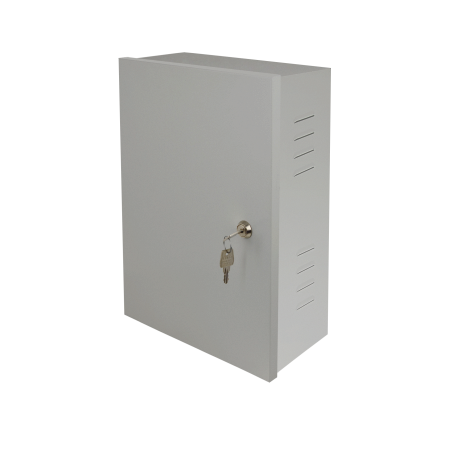
grey - structure RAL 7035
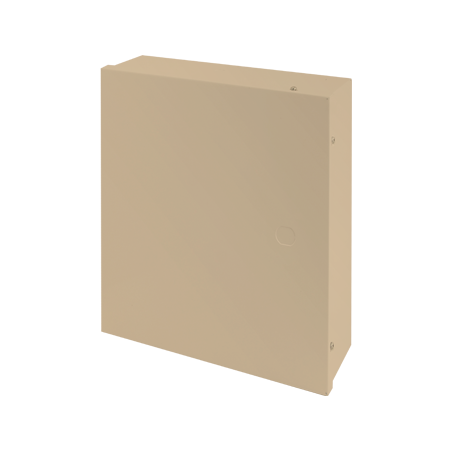
beige - structure RAL 1001
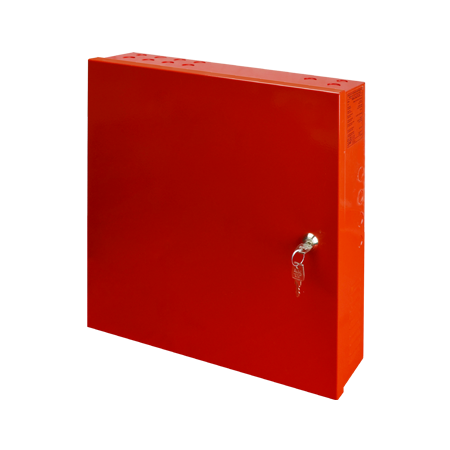
red - structure RAL 3001
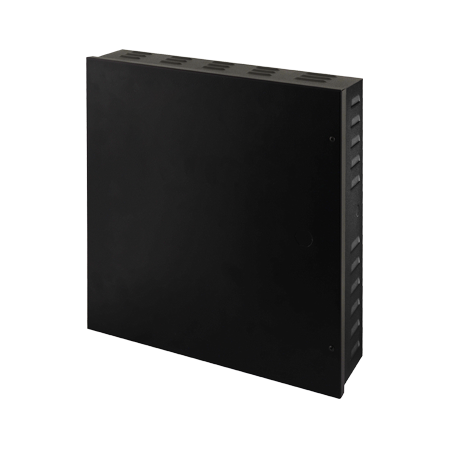
black - structure RAL 9005
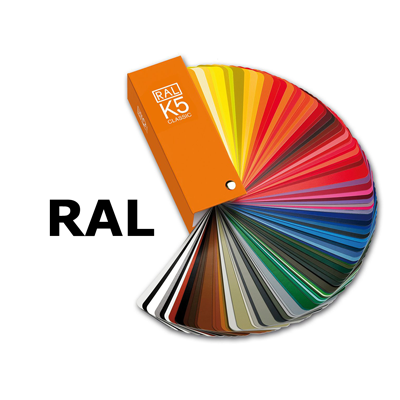
other colours per request
Enclosure designs
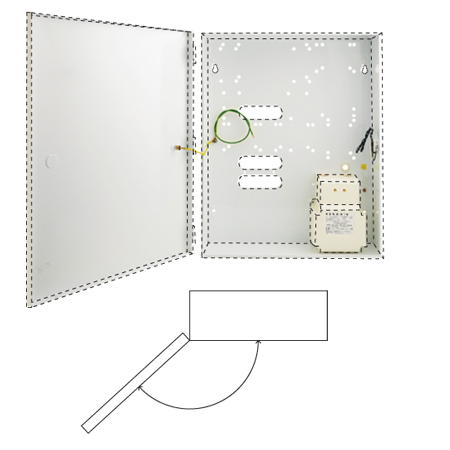
”KO-1”
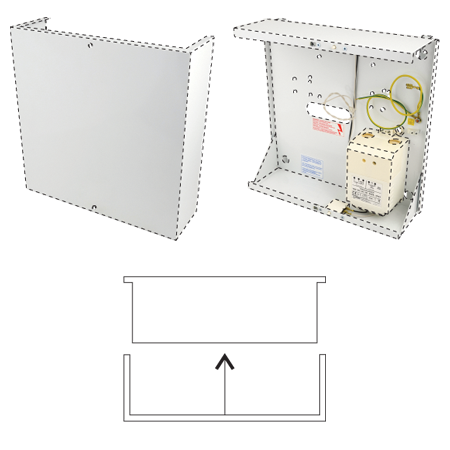
removable front cover ”KO-2”
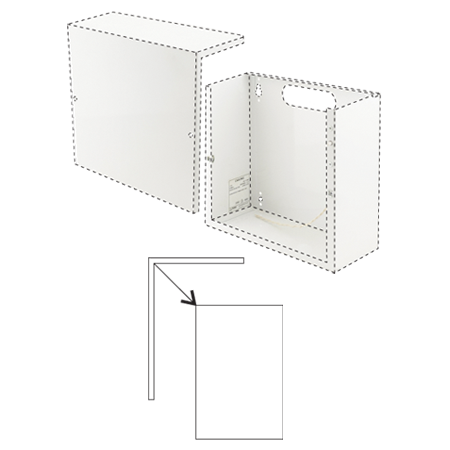
removable front cover ”KO-3”
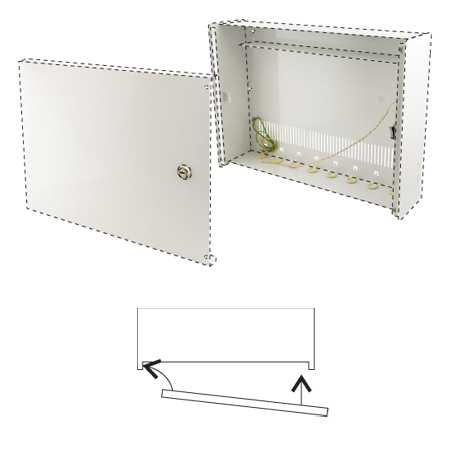
”KO-4”
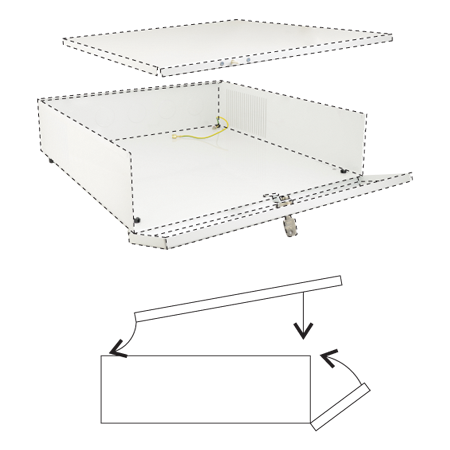
”KO-5”
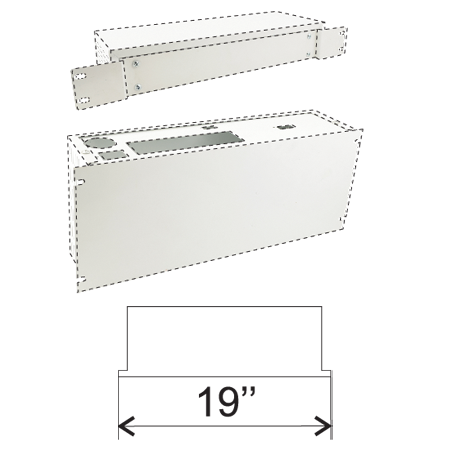
RACK 19″ type ”KO-6”
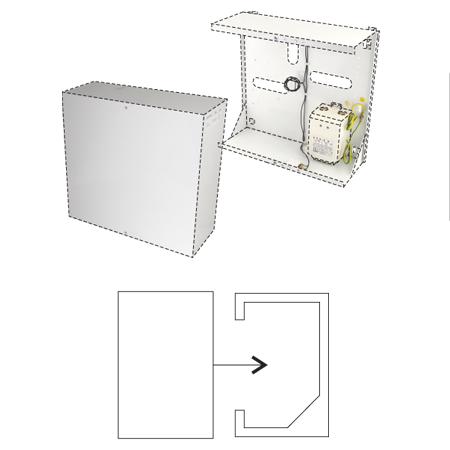
removable front cover ”KO-7”
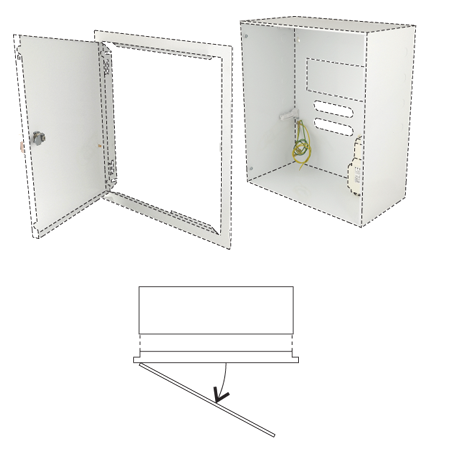
”KO-8”
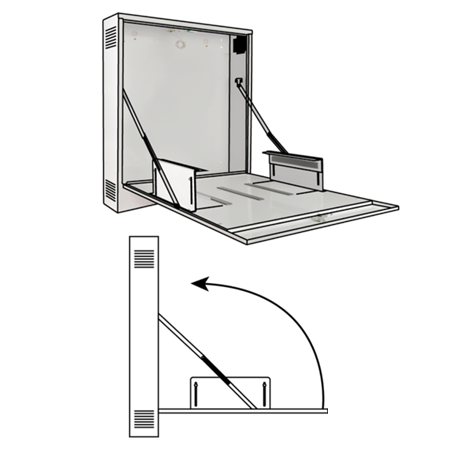
”KO-9”
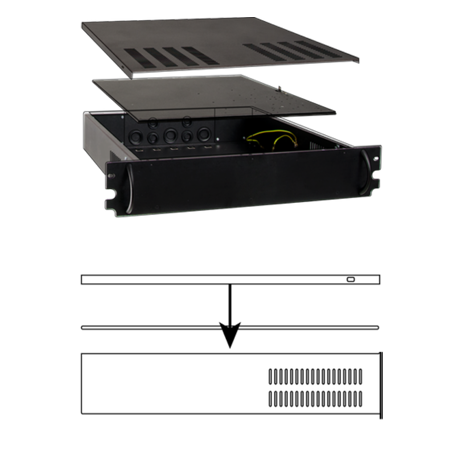
Removable RACK19" type ”KO-10”
Lid design
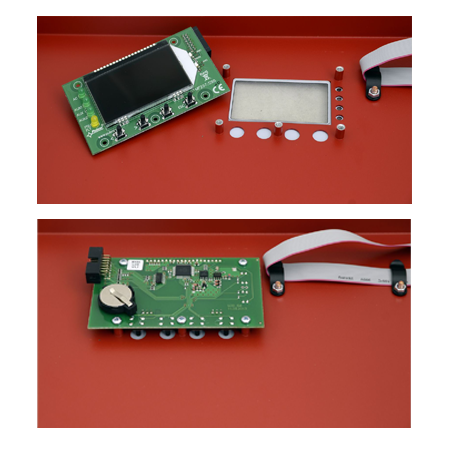
holes for micro switches, diodes, LED and LCD displays
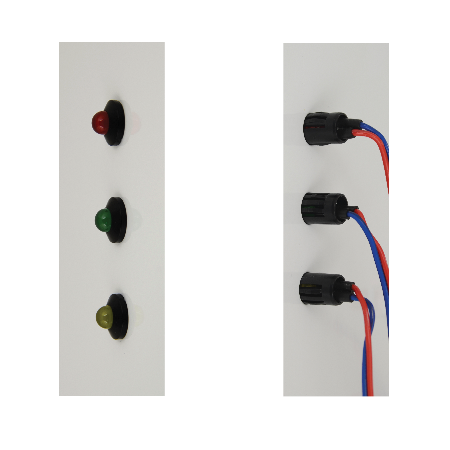
LED fittings
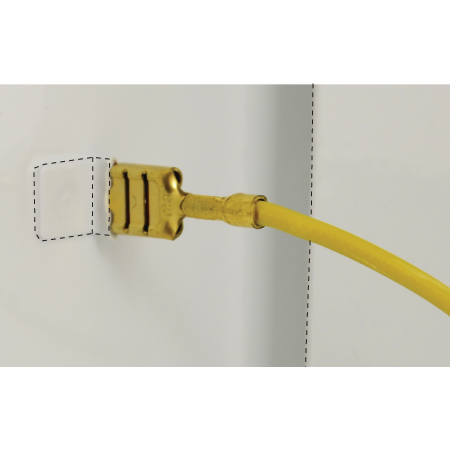
UZ-1 type
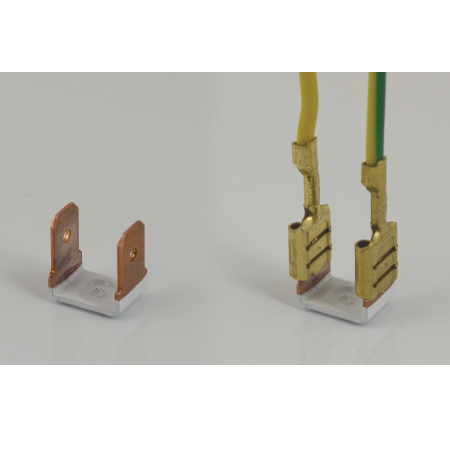
UZ-2 type
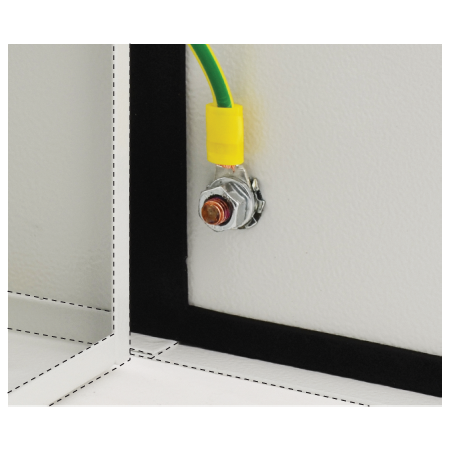
UZ-3 type
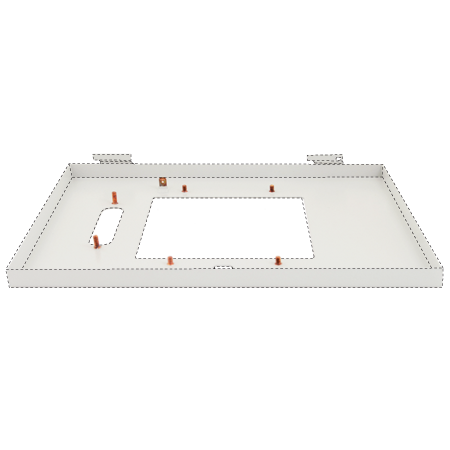
holes in lid
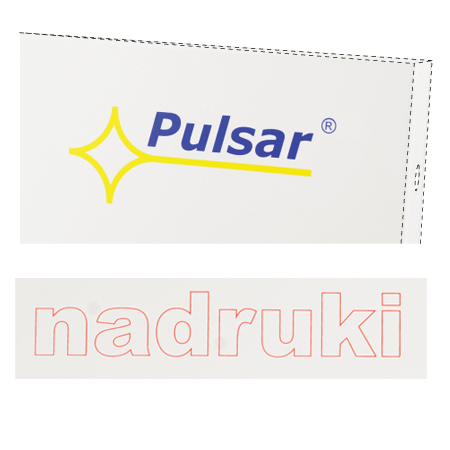
Prints in various colours according to RAL
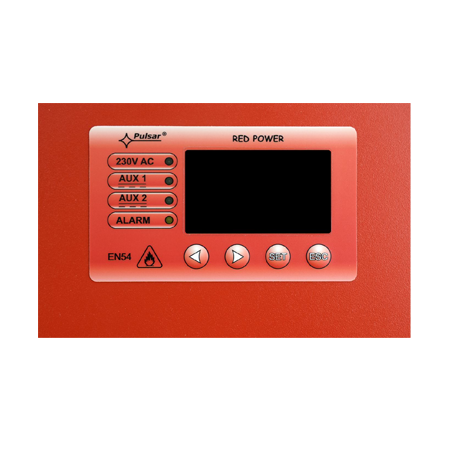
stickers
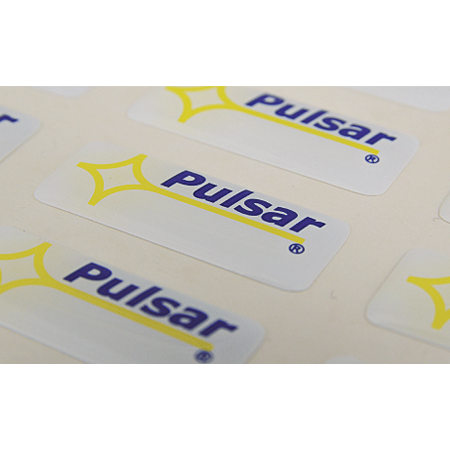
3D stickers
Hinges
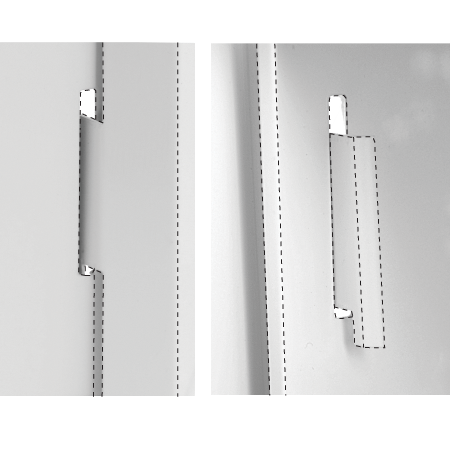
MC-1 type Removable hinges
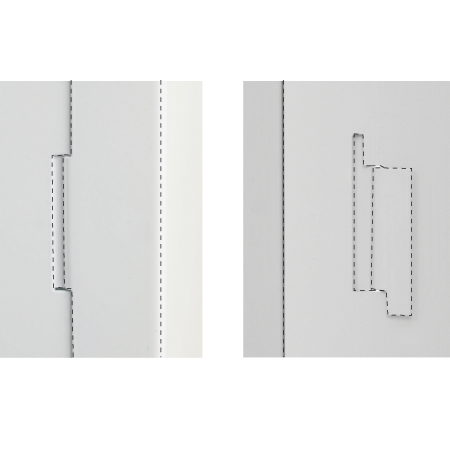
MC-2 type Gapless removable hinges
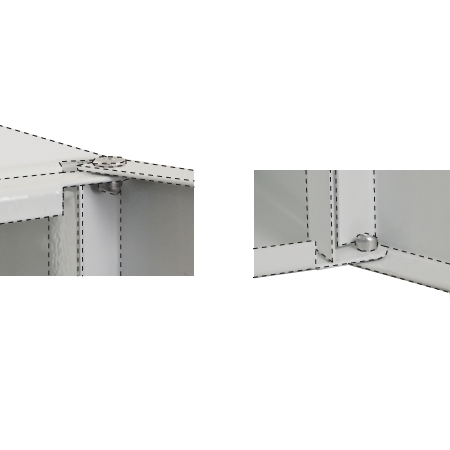
MC-4 type Rivet hinges
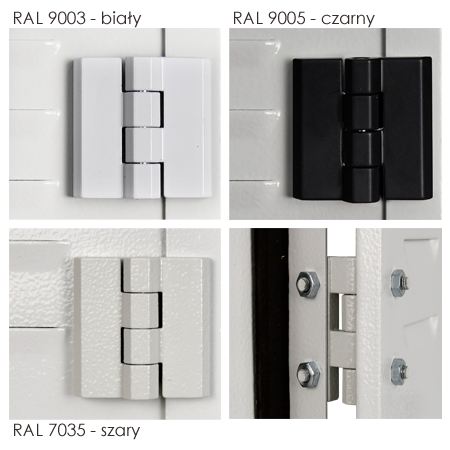
MC-5 type Screwed hinges
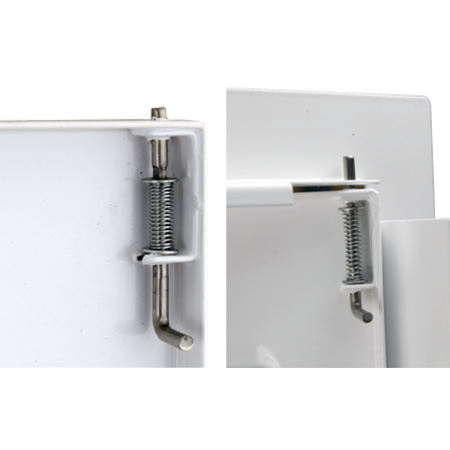
MC-6 type Sliding hinges with spring
Lid closing
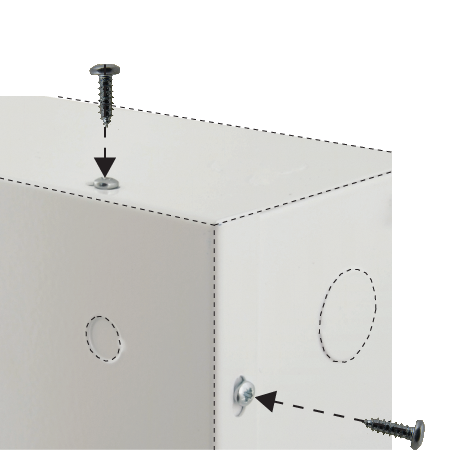
ZC-1 type Screwed
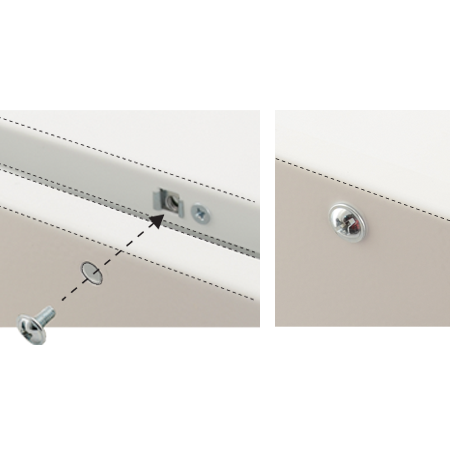
ZC-2 type front side mounting (Clipko M3, M4)
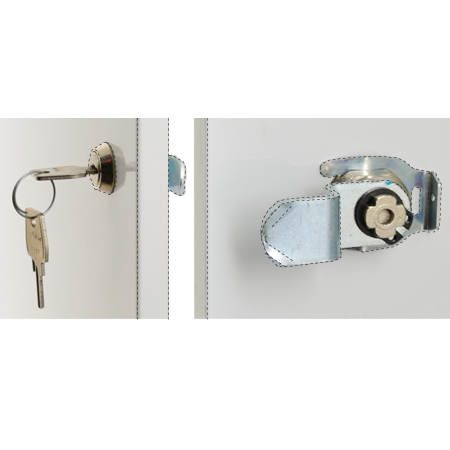
ZC-3 type metal lock with key
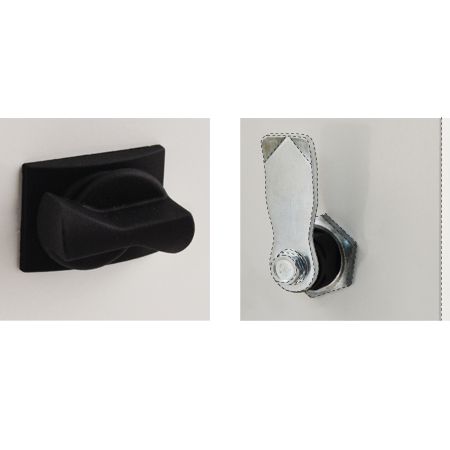
ZC-4 type Plastic lock without key
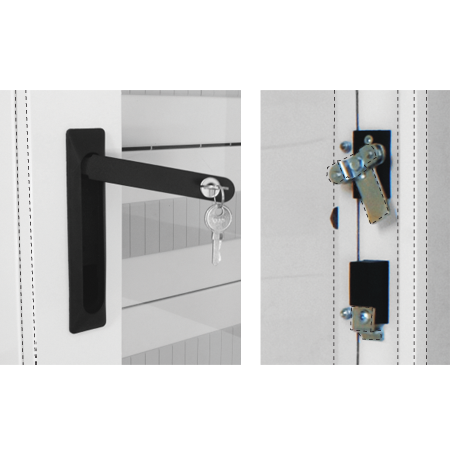
ZC-5 type Plastic lock with key
Distance from the wall
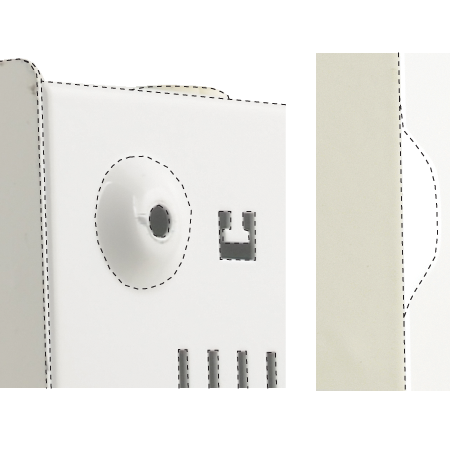
Metal spacer
5mm DS-1A type
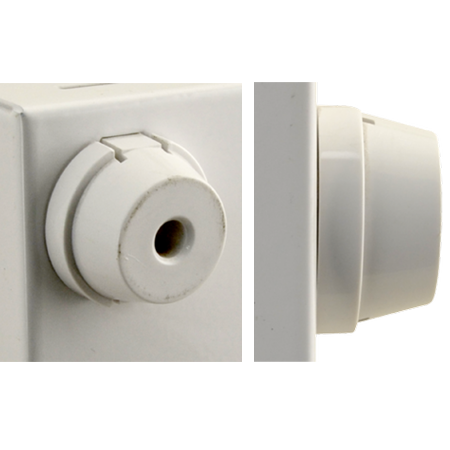
Plastic spacer
11mm DS-1B type
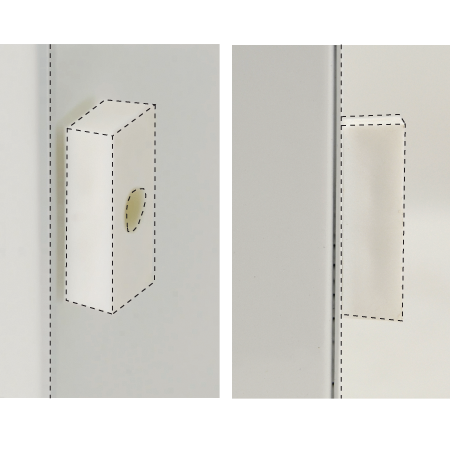
Plastic spacer
8mm DS-2A type
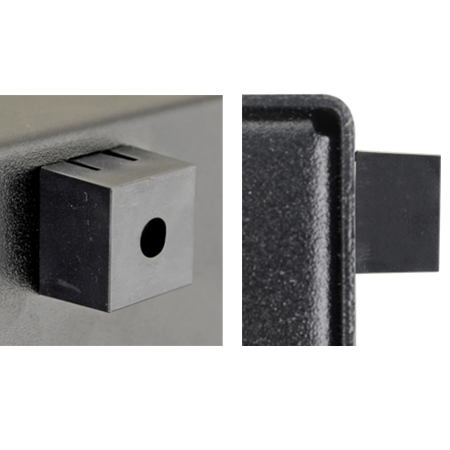
Plastic spacer
14mm DS-2B type
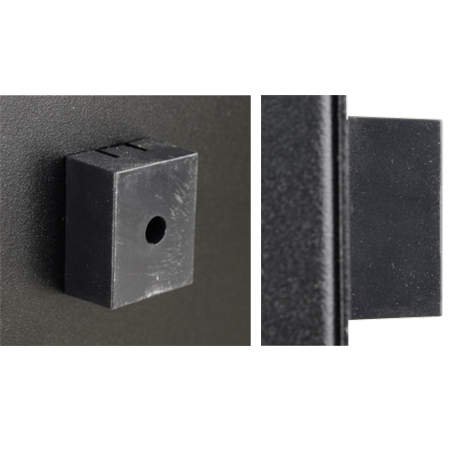
Plastic spacer
14mm DS-2C type
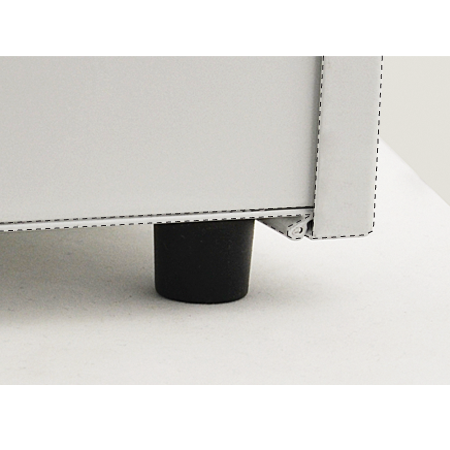
Feet in self standing enclosures
DS-3 type
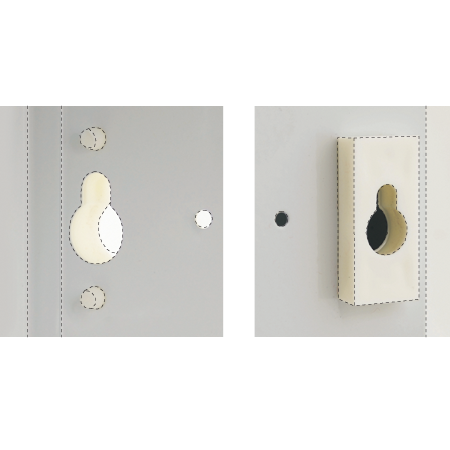
Plastic spacer – 8mm
DS-4A type
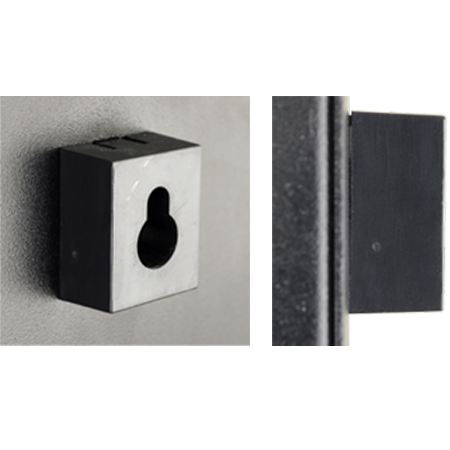
Plastic spacer – 14mm
DS-4B type
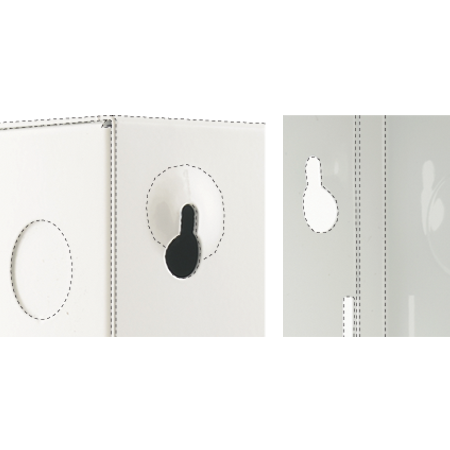
Metal spacer – 5mm
DS-5 type
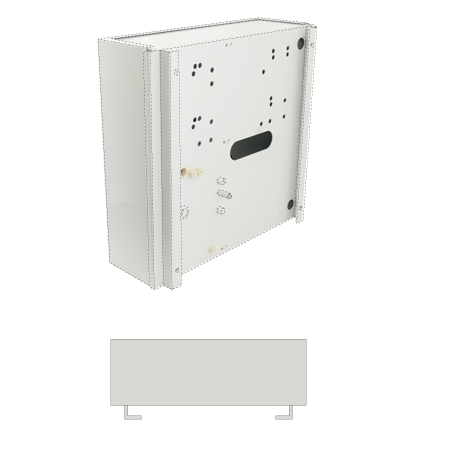
Rail type spacer
DS-6 type
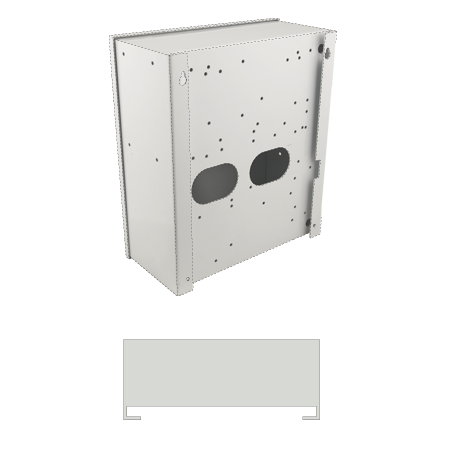
Rail type spacer
DS-7 type
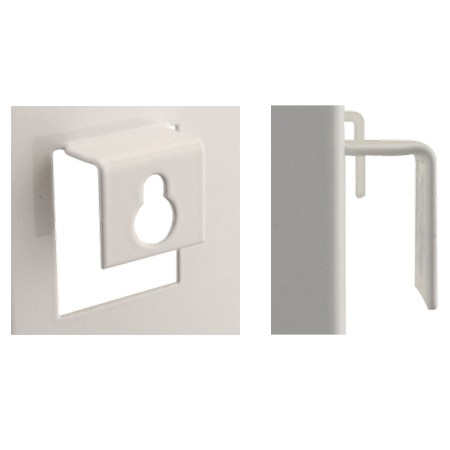
Metal spacer 10mm
DS-8A type
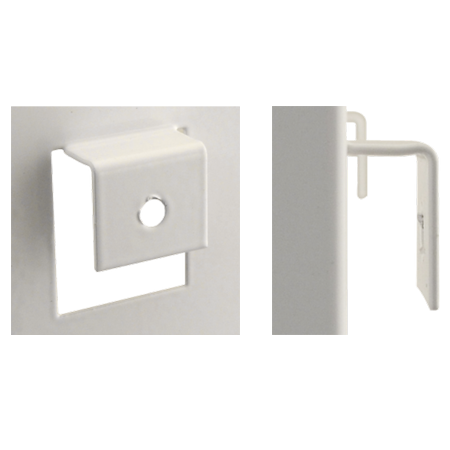
Metal spacer 10mm
DS-8B type
Enclosure equipment
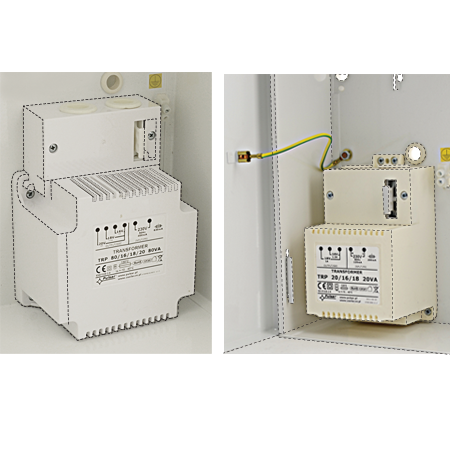
transformer TRP series - IP30
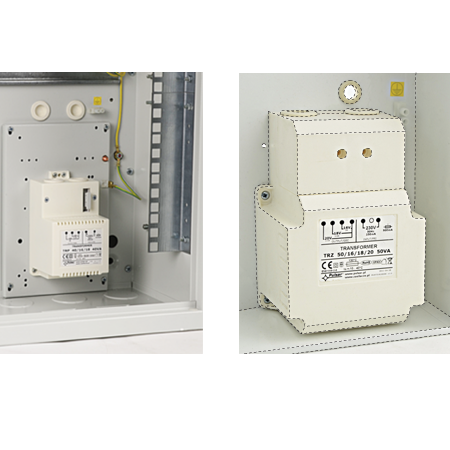
transformer TRZ series - IP43
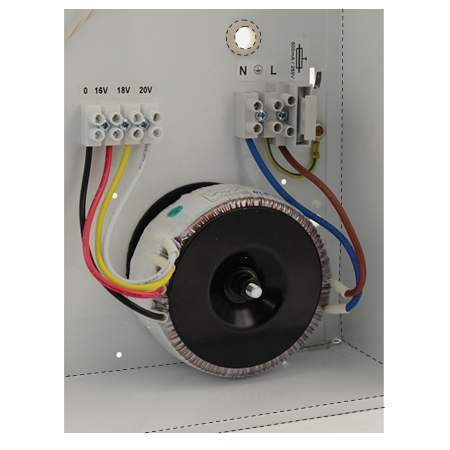
transformer TOR series
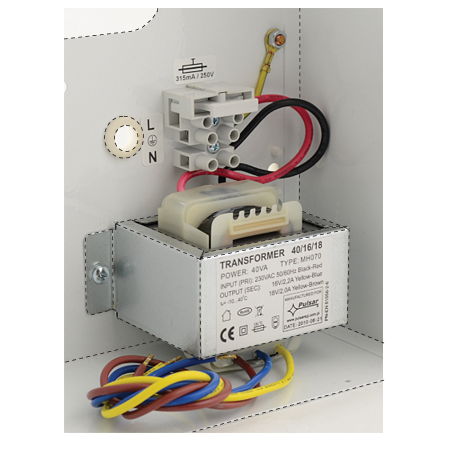
transformer EI series
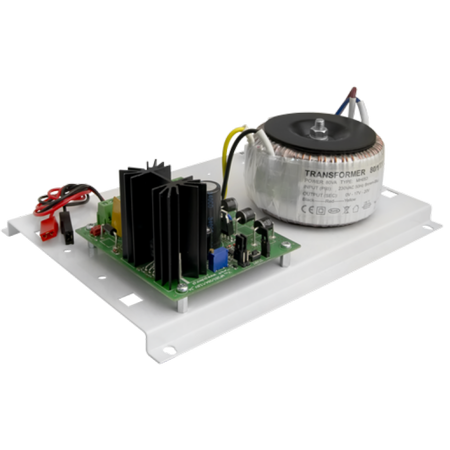
Power supply units
Open frame
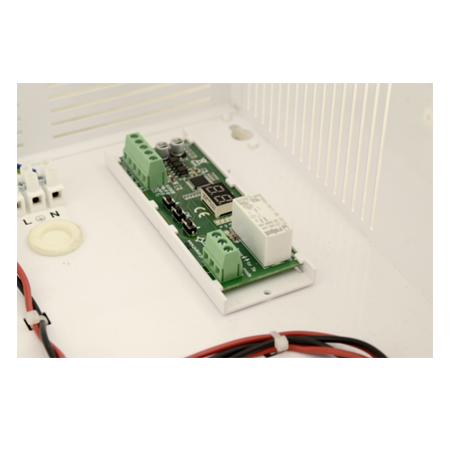
electronic modules
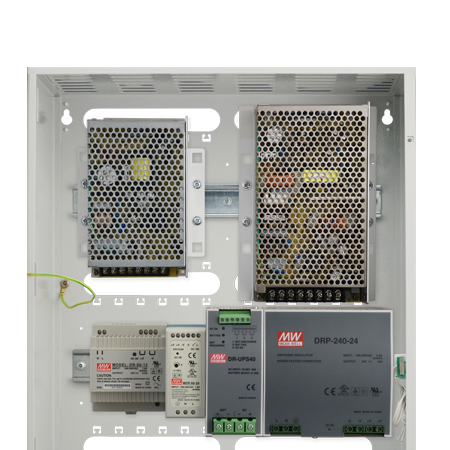
Power supply units
for DIN rail
MEAN WELL Company
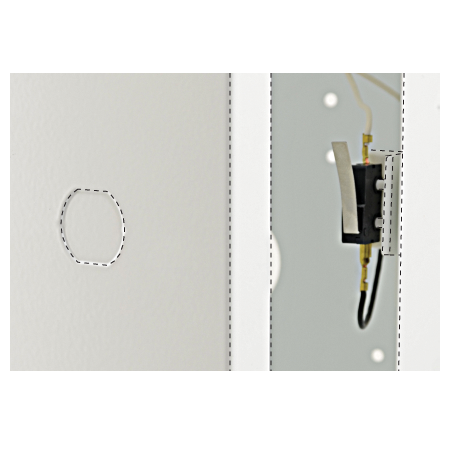
tamper switch
unwanted enclosure opening
TP-1 type
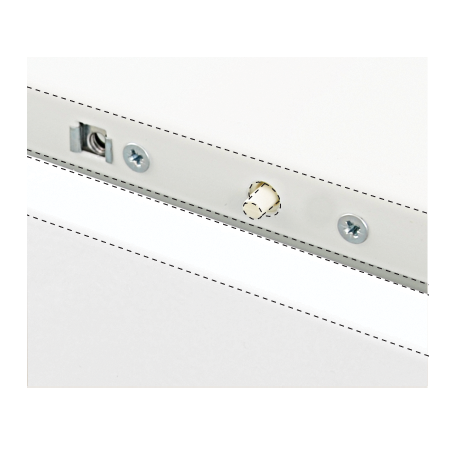
tamper switch
unwanted enclosure opening TP-2 type
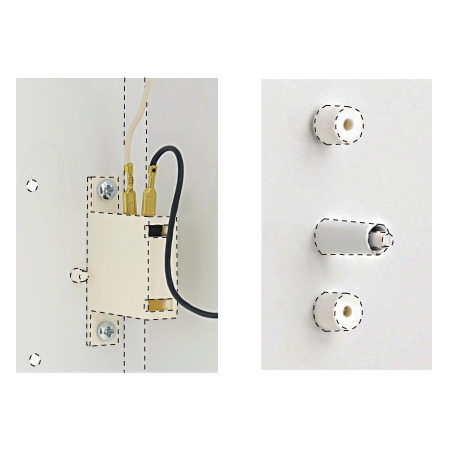
tamper switch
enclosure detachment
in metallic cover TP-3 type
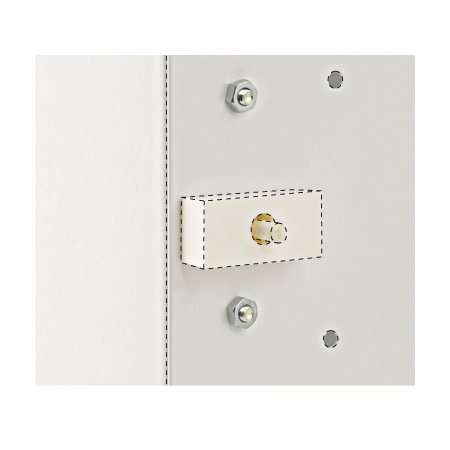
tamper switch
enclosure detachment
in a plastic cover TP-4 type
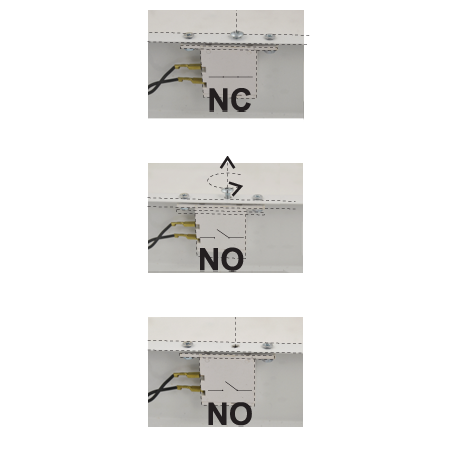
tamper switch
TP-5 type
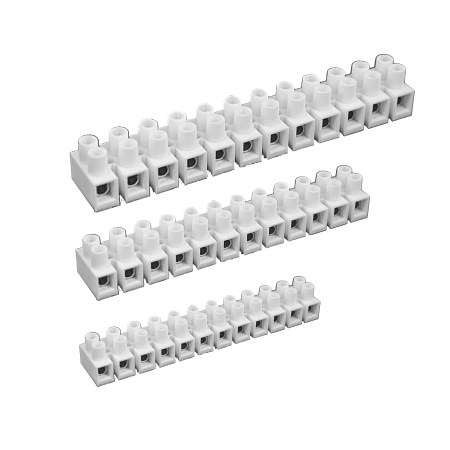
12-way connector strips 2,5 / 4 / 6 mm2
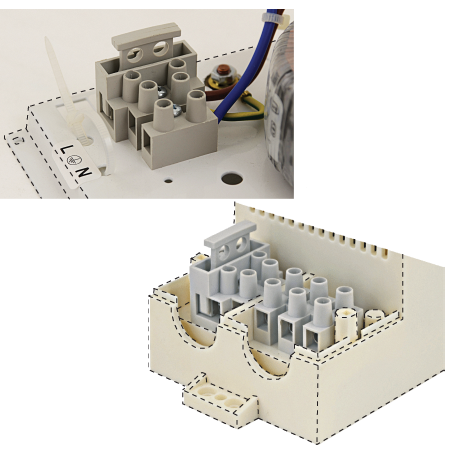
terminal block with fuse: 3 or 5
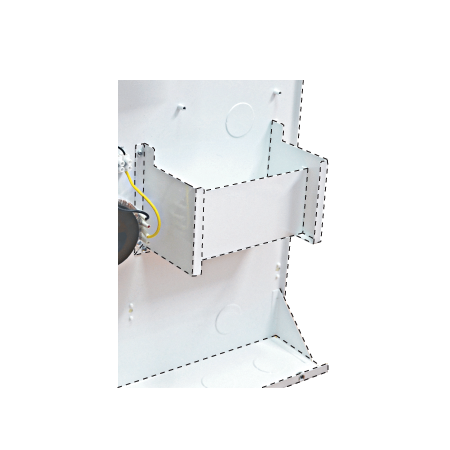
shelves mounted permanently
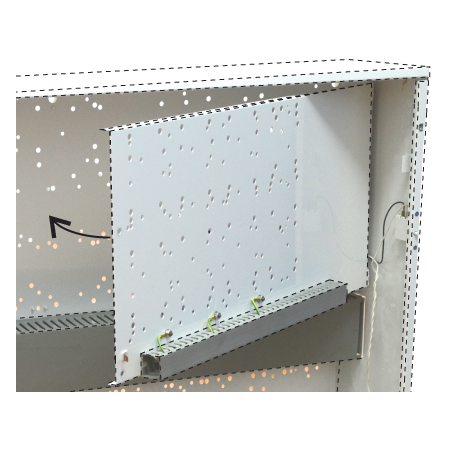
hinged mounting plate

enclosure grounding

cable trays
Installation of equipment
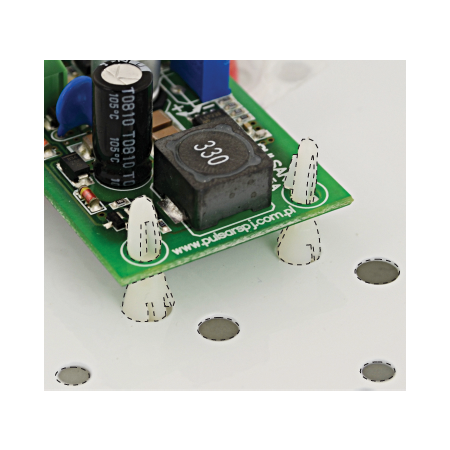
holes + pins
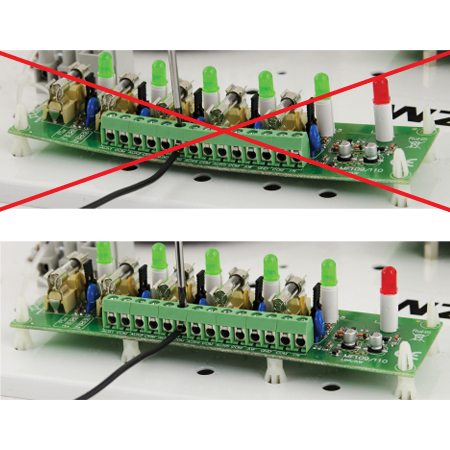
PCB support
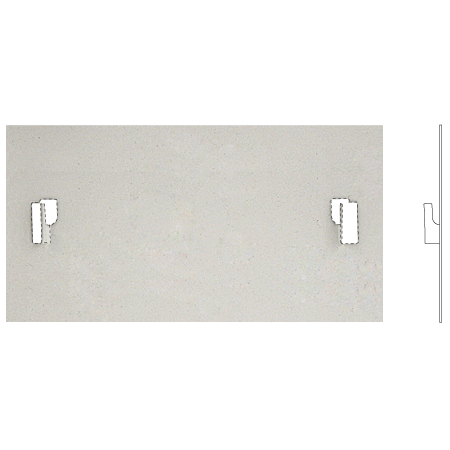
hangers
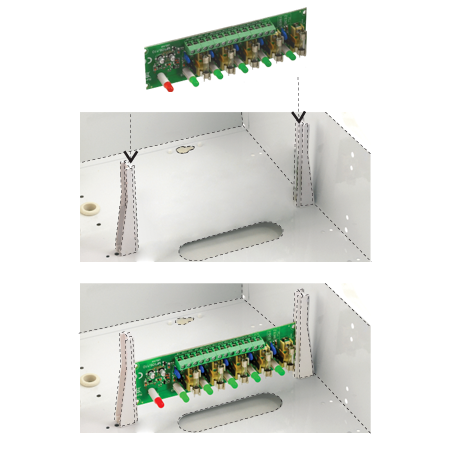
mounting on GE vertical slides

pressed-in threaded pins – FH
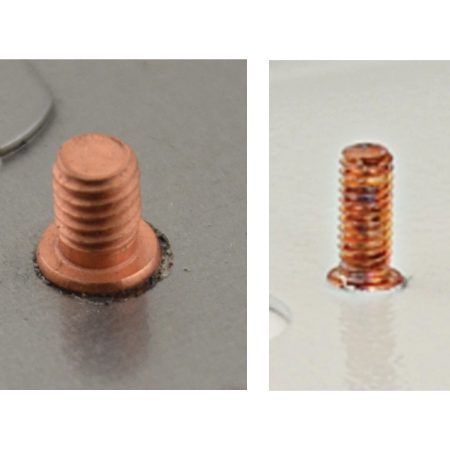
welded threaded pins – ST
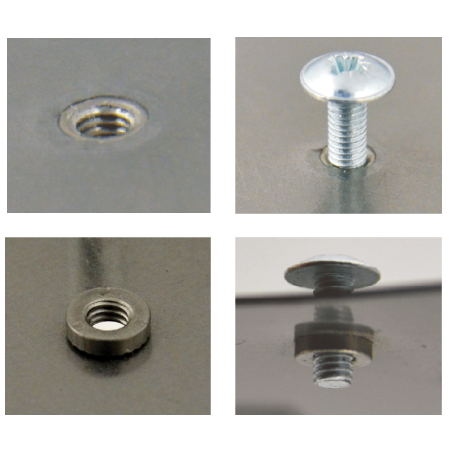
SMPS threads
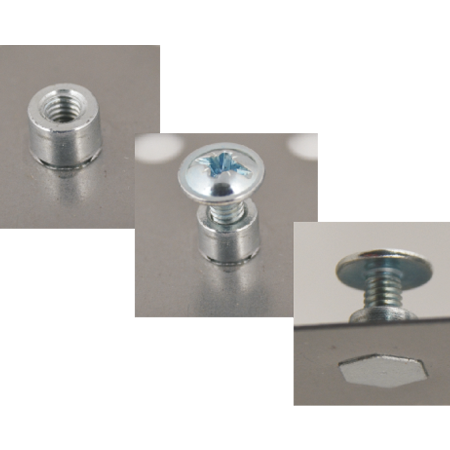
pressed-in threaded sleeves, non-through BSO type
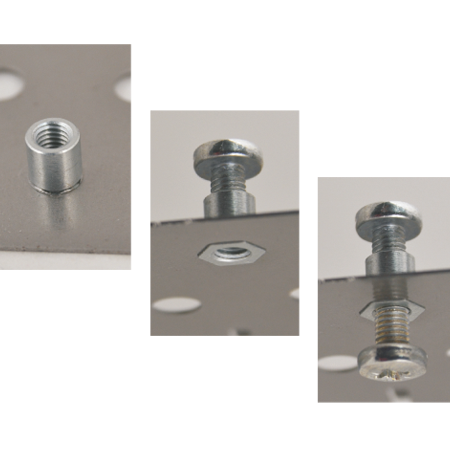
pressed-in threaded sleeves, through SO type
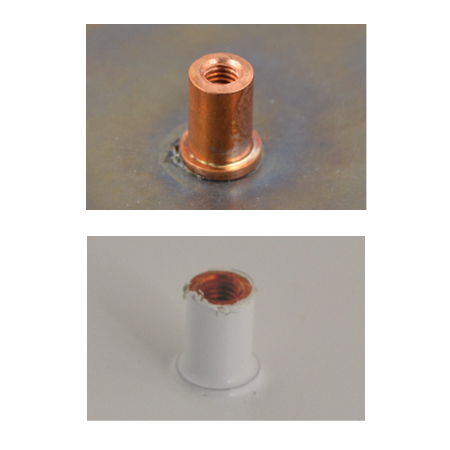
pressed-in threaded sleeves – ST
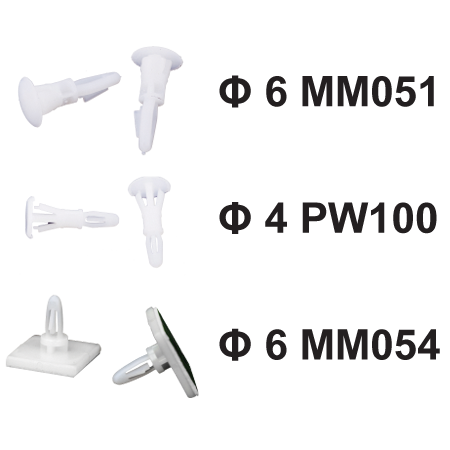
PCB plastic pins
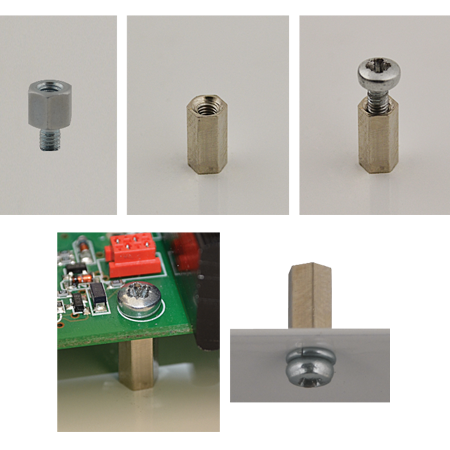
male/female hex spacers M3x10
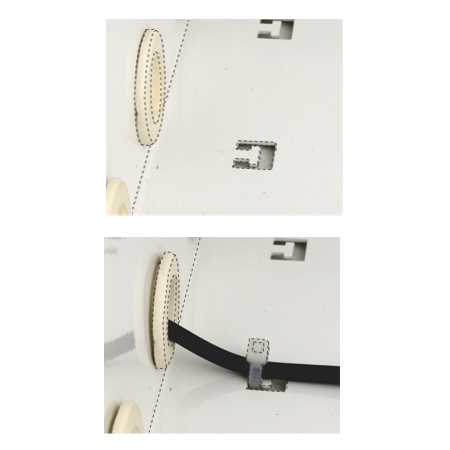
openings for cable ties
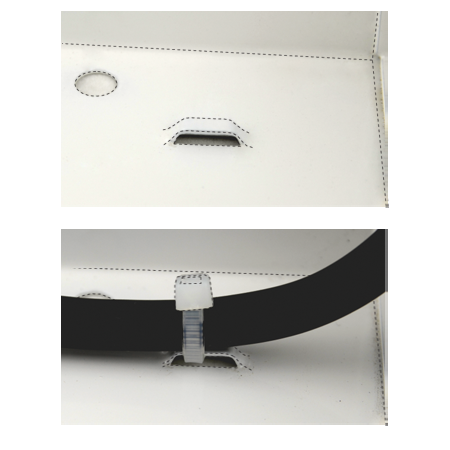
openings for cable ties
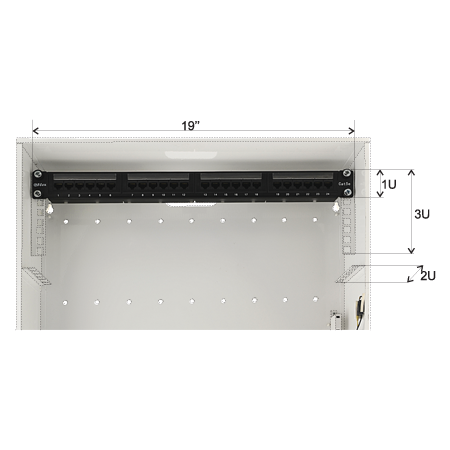
RACK type mounting
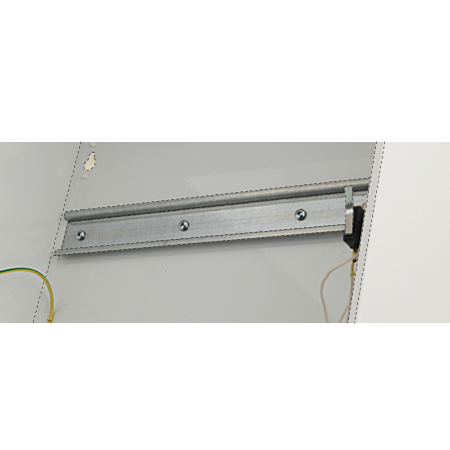
screwed DIN rail
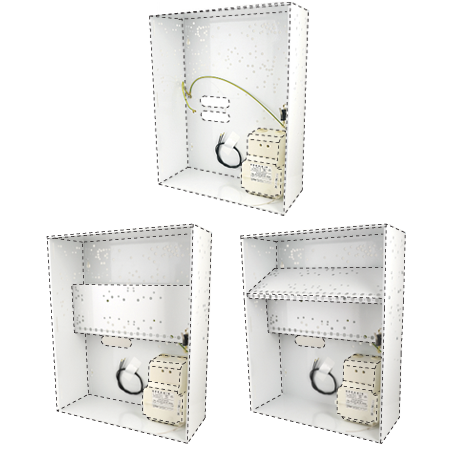
mounting on shelf
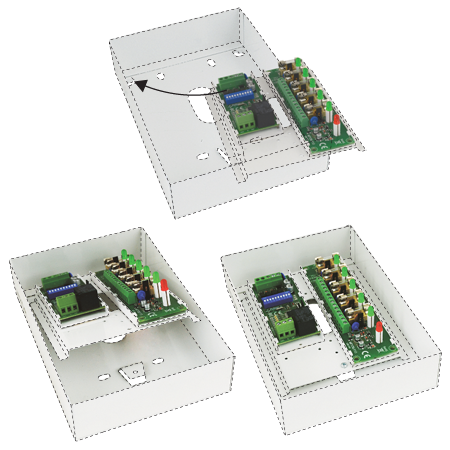
mounting on mounting plate
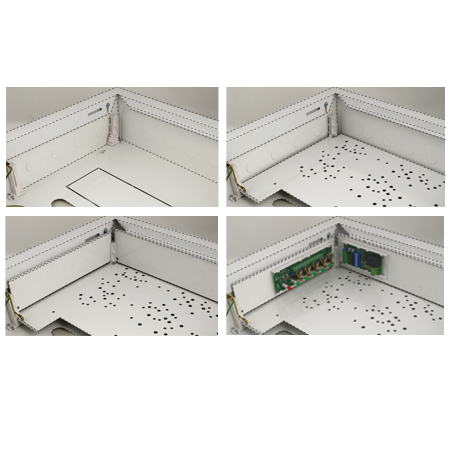
mounting on side mounting plate
Ventilation
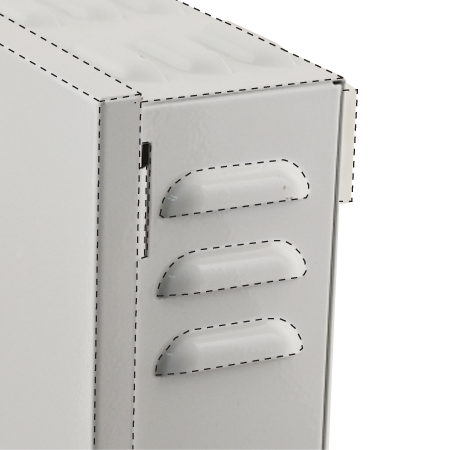
„The „Gills” ventilation” – WT-1 type
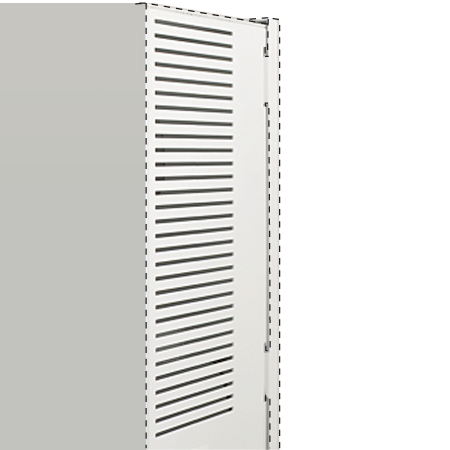
rectangular holes – WT-2 type
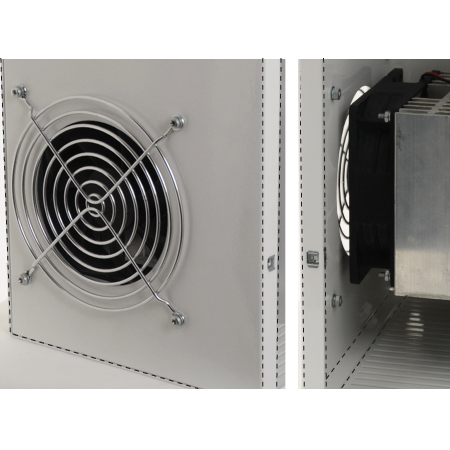
Fan protection – WT-3 type
Cable entries
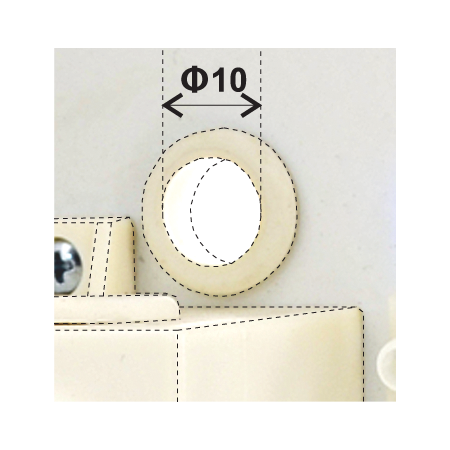
rubber grommets Ø10
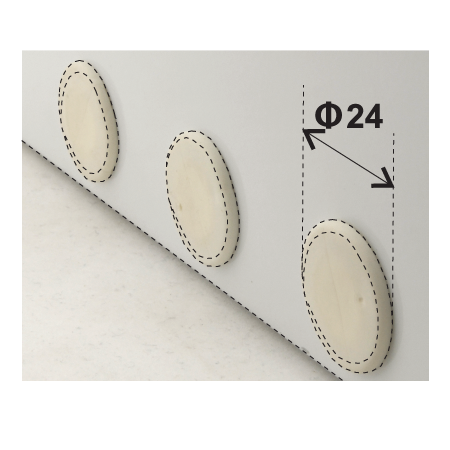
full rubber grommets Ø24
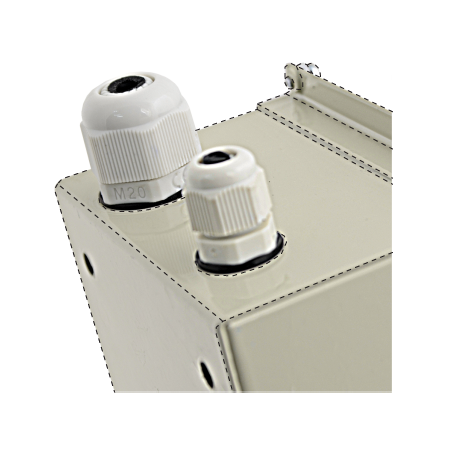
glands IP68, M20, M16, M12
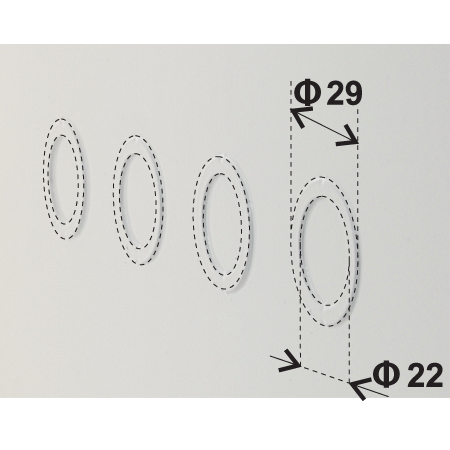
double embossing for punching Ø29/22
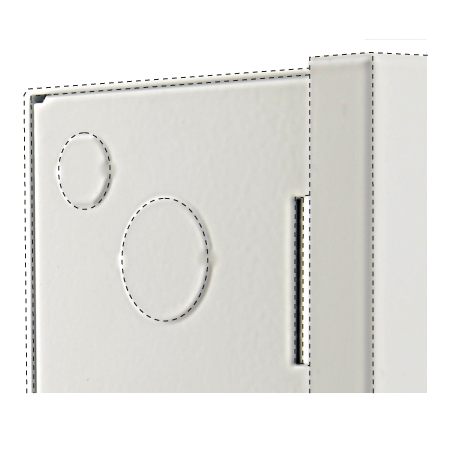
round embossing for punching
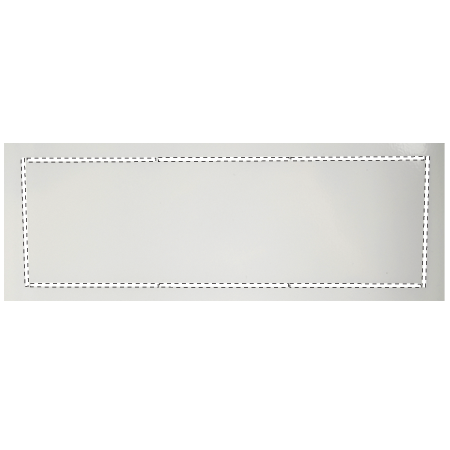
rectangular embossing for punching
Openings / Embossings
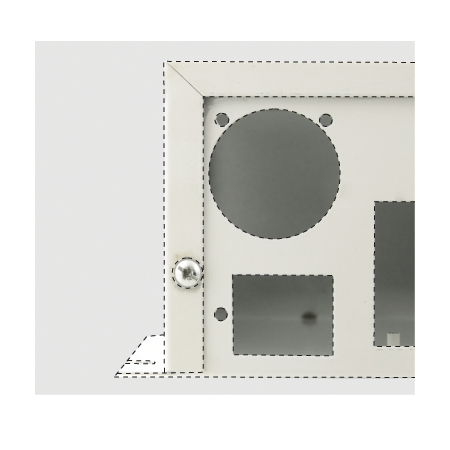
round holes, rectangular holes
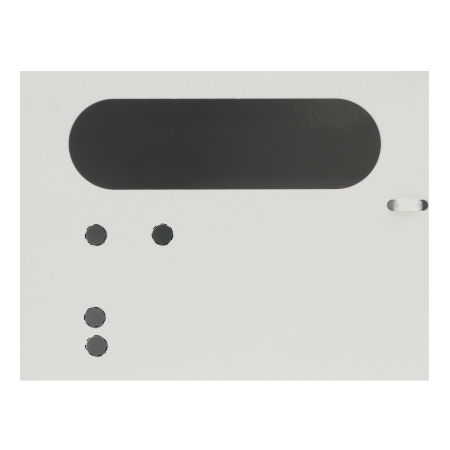
ellipses

other shapes
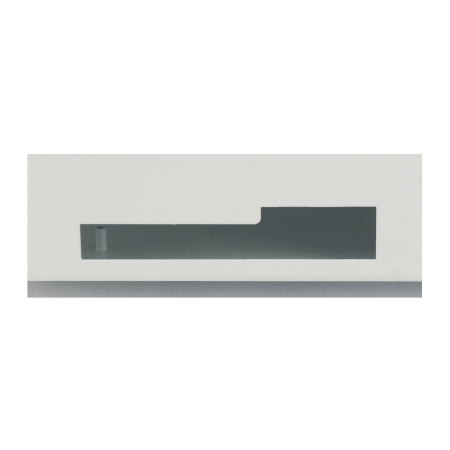
other shapes
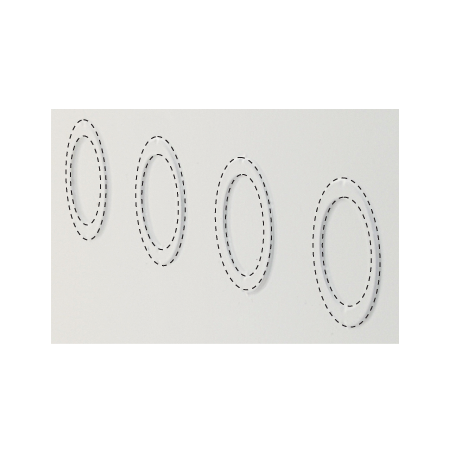
embossing
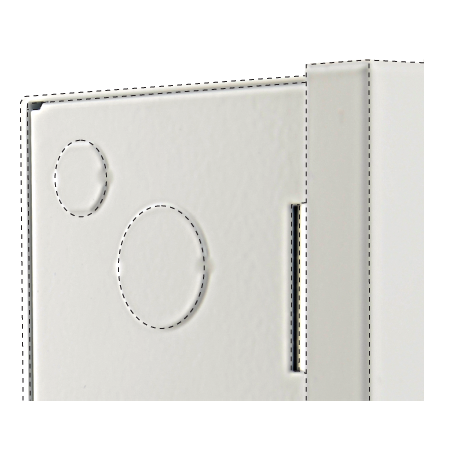
embossing for glands
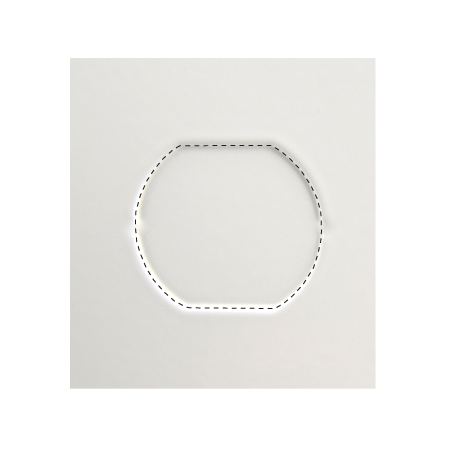
embossing for a lock
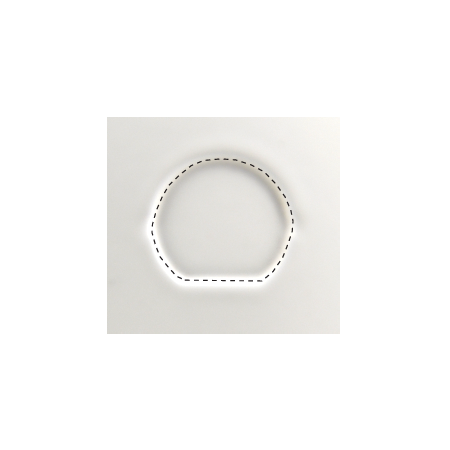
embossing for GSM antenna
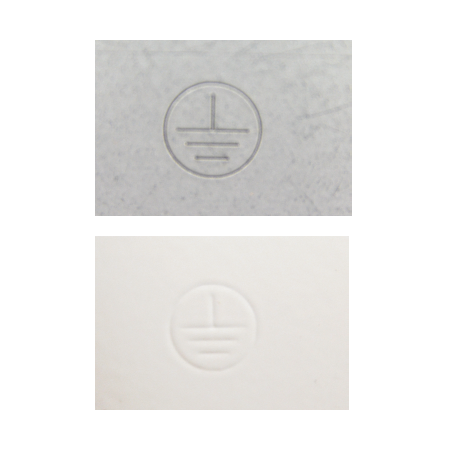
Grounding symbol
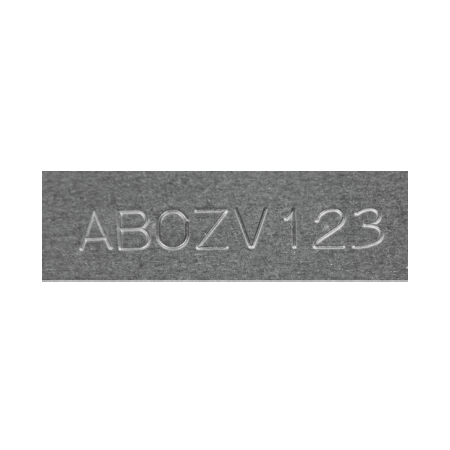
names and numbering
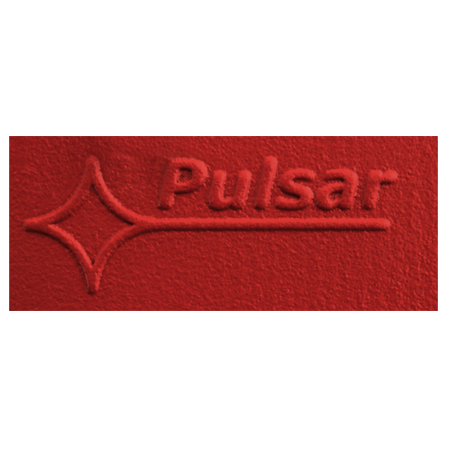
logo
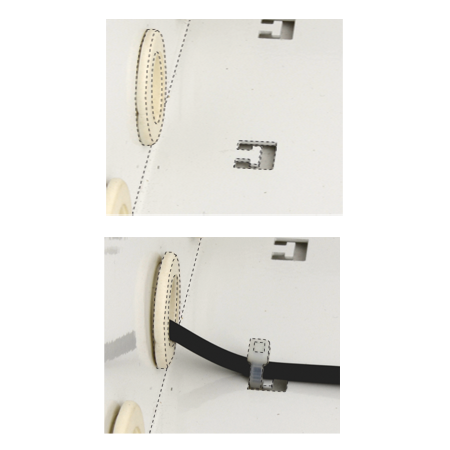
Openings for cable ties
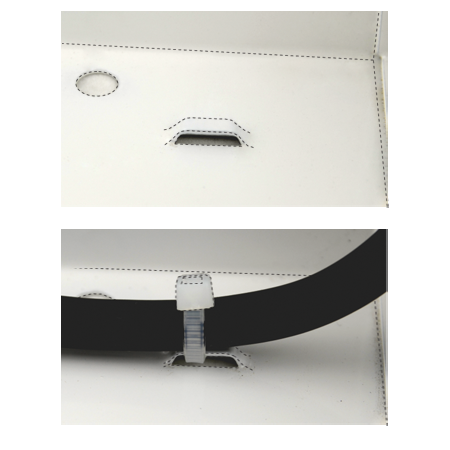
Pre-embossed opening for cable ties
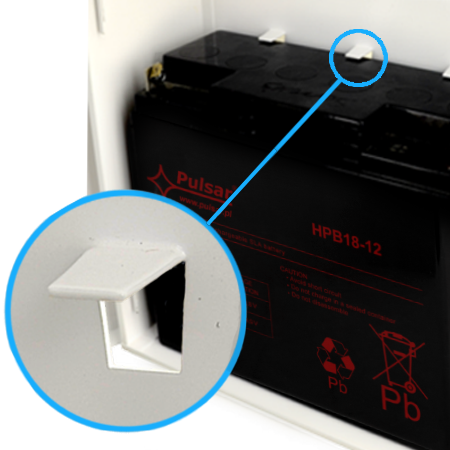
Limiting embossing
Examples of enclosures
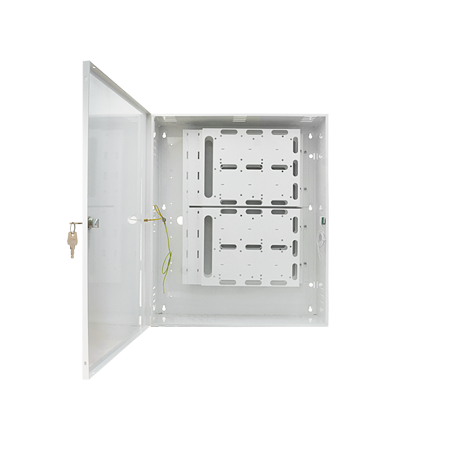
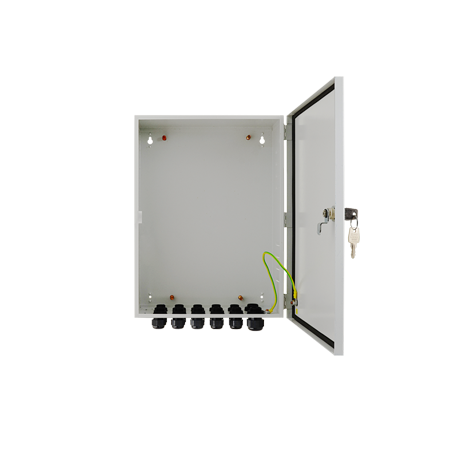
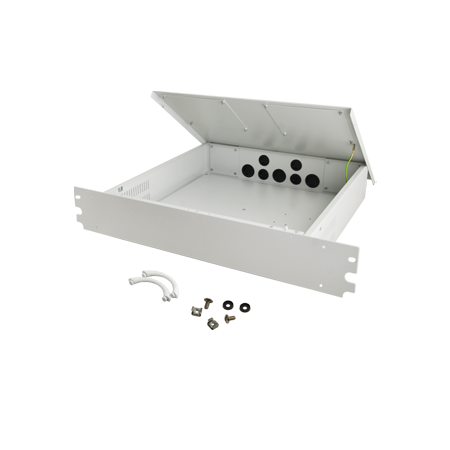

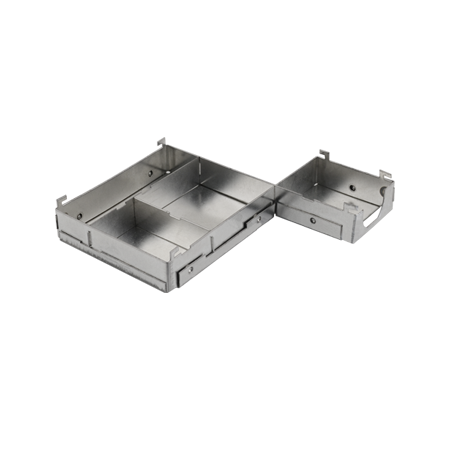
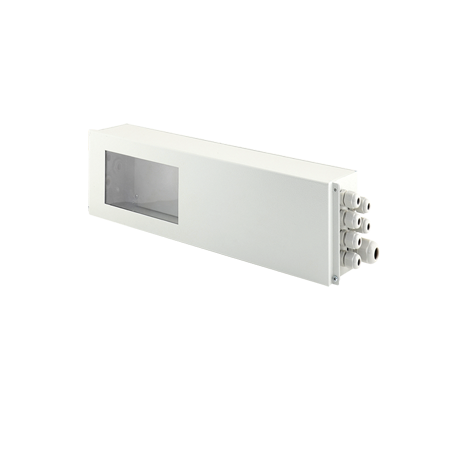
Examples of power supply units

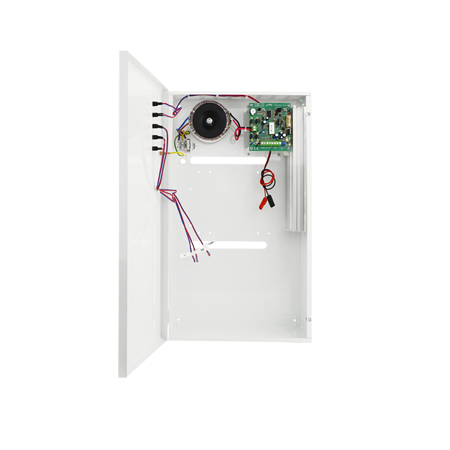
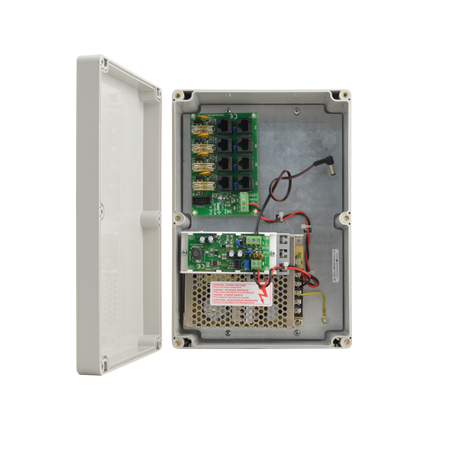
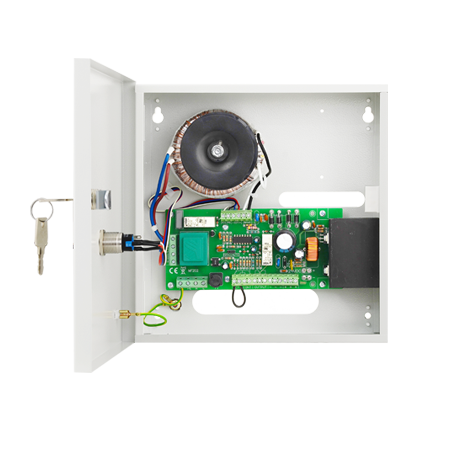
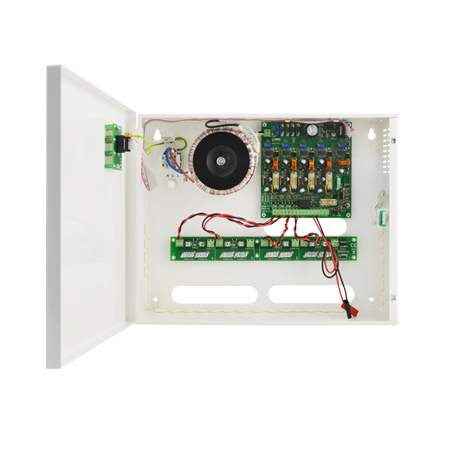
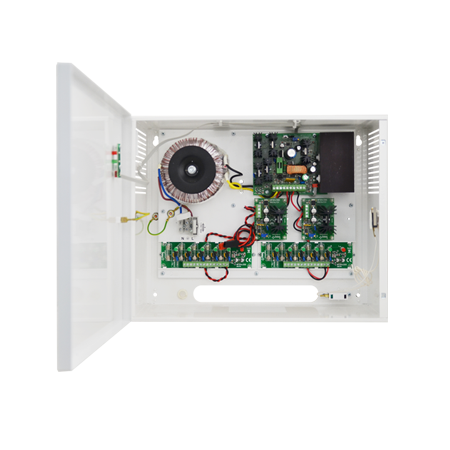
See how our products are made
Welcome to our website about the production of electronics and enclosures. Custom projects of electronics design, installation and comprehensive production of electronic devices (OEM and ODM). Our professional customer service has earned us the trust of customers in Poland and abroad. We are pleased to invite you to cooperate with our company.
Loading...
1. Designing
2. Automatic Screen Printer
3. Automatic SMD
4. Tunnel furnace
5. Through-hole technology
6. Soldering unit
7. Wire processing
8. The production of transformers
9. Electronics
10. EMC Laboratory
11. Temperature test chamber
12. obudowy
13. Screen printing
14. Injection molding machines
15. 3D printer
16. Electronics assembly
17. Storage and Shipping
1. Designing
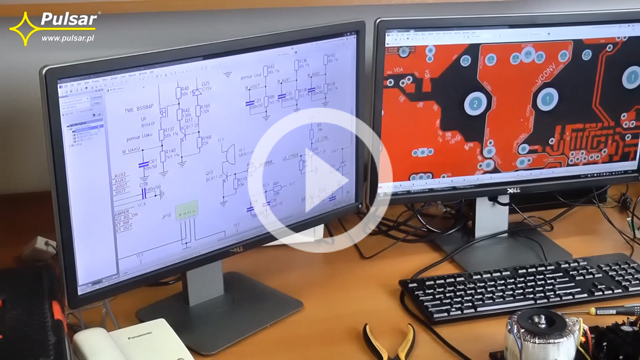
Our engineering staff designs complex electronic products. The design process involves many stages, of which the most important include the development of a schema, designing a PCB circuit (taking into account EMC requirements) and functional, thermal, and EMC testing. The design process is also based on integrated development environments, providing support in processor systems engineering and software design. We also offer technical advice, custom projects and professional service.
2. Automatic Screen Printer
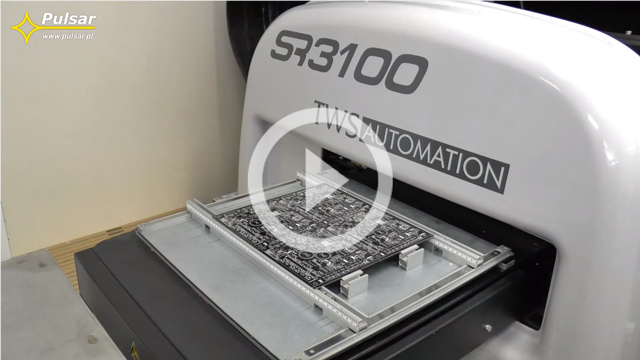
The first step on the SMT (surface mount technology) assembly line is applying solder paste and/or glue on printed circuit boards. This process is carried out using the SR3100 screen printer manufactured by TWS Automation. Precise steel mesh along with the measurement of reference points allows the accurate adjustment of the position of the screen in relation to the PCB. The automated process for applying solder paste allows uniform coating of soldering points which is reflected in the quality of solders.
3. Automatic SMD
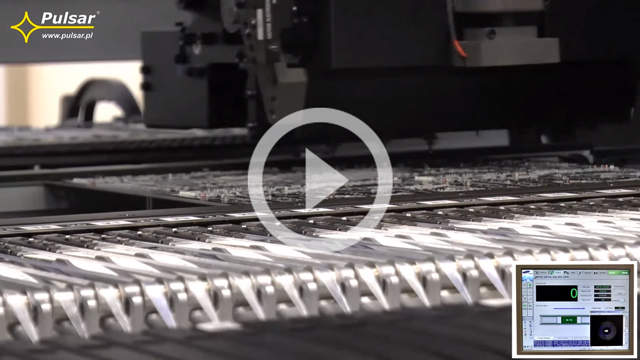
We offer professional mounting of SMD on printed circuit boards. The process is performed with the use of the modern, precise and highly efficient SAMSUNG SM482 SMD machine. The use of high-quality machine, strict production procedures, and our senior technicians guarantee the quality of our services. SMD or Surface Mount Electronic Components are placed in special containers, picked up from the feeders/tray by a system of nozzles and then placed on the appropriate pads on the PCB. The vision system allows to place individual components on the appropriate pads on the PCB with high precision. The minimum size of the components is 0402 (a rectangle of 1. 0mm x 0.5mm). The machine's performance reaches up to 28 000 SMD components per hour.
4. Tunnel furnace
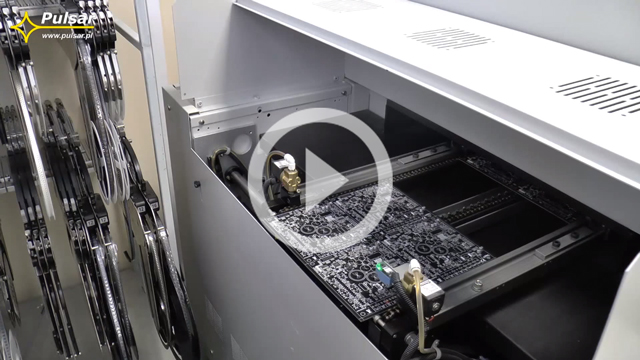
The 1707 Mark III Series - SMT Reflow Oven is an essential element of SMT lines. It is a modern, convection tunnel klin with 7 heating zones. The solder paste is heated and melted in different zones of the furnace. In addition, loads (stresses) on the solders (SMD soldered to PCB pads) are also reduced. Conveyor System transporting PCB in the oven guarantees full control over the soldering process and process repeatability for each PCB.
5. Through-hole technology
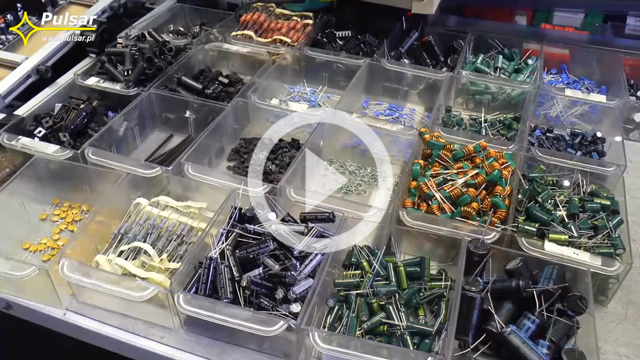
In Through-Hole Technology, leads are soldered manually at individual workstations. It requires the appropriate assembly of components, iincluding: electrolytic capacitors, coils, inductors, diodes, and transistors with heatsinks. Then, wave soldering is used to soldering through-hole components on the bottom of PCB.
6. Soldering unit
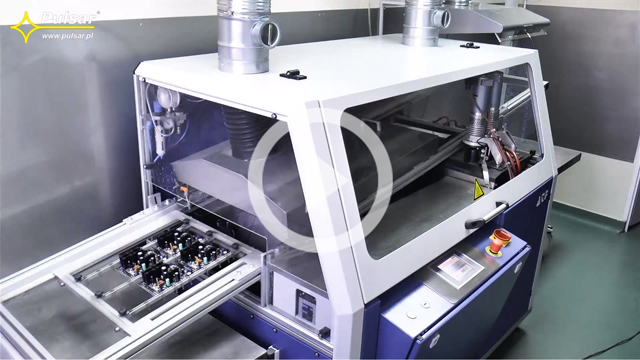
PCBs are sent to a modern soldering unit by ATF. Then, the tin-plating of printed circuit boards and soldering through-hole components (through-hole technology – THT) on the bottom of PCBs, is performed. This leads to lead-free soldering in a nitrogen atmosphere. The use of nitrogen reduces oxidation and improves the quality of soldering. 90% of the soldering process is performed automatically, the remaining 10% is additional manual soldering.
7. Wire processing
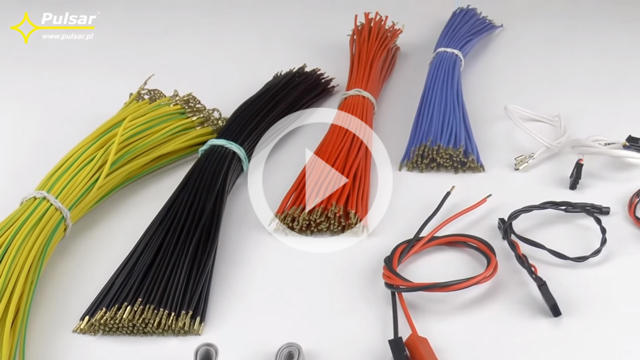
The Gamma 263 S crimping machine by KOMAX enables fully automatic wire processing. The device precisely cuts wires to a desired length and allows one and two-sided crimping. The maximum cross-section of the processed cable is up to 4mm2 with cable lengths from 4 cm to 20 m. Full control of the quality of the crimped connector is ensured by the certified Universal Tester Model CT 50 by MAV PRÜFTECHNIK for tensile strength measurements. Indication range: 0-500 N.
8. The production of transformers
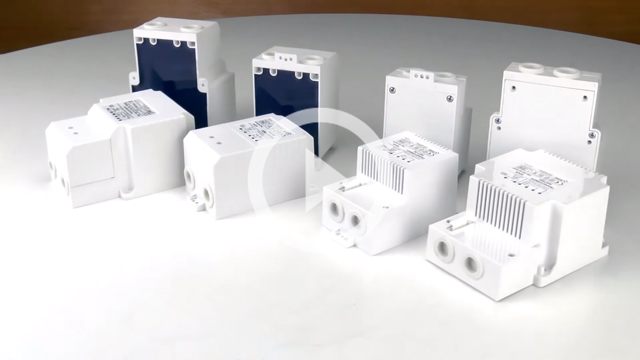
Our company offers transformers of the following series: T (IP43), TRP (IP30), TOR, and EI with power ranging from 20 VA to 300 VA. Transformer enclosures (TRZ, TRP) are made of PC/ABS, UL 94 V-0 class. Transformers of the TRZ series, cast epoxy resin, IP43 protection class. In the final stage of the production process, transformers undergo a number of tests. These include, among others, high-voltage AC dielectric test and DC insulation resistance measurement using the certified MI 2094 CE Multitester by METREL.
9. Electronics
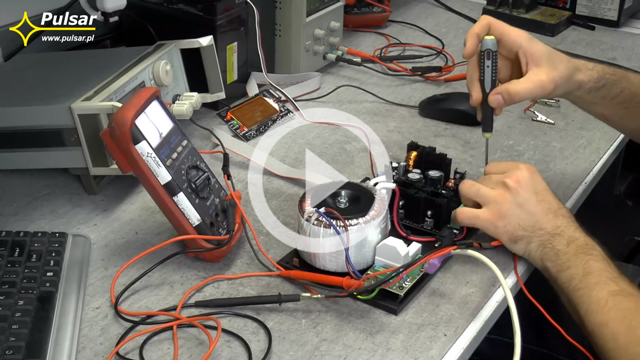
The next step in the production process is programming and testing of electronics. Firmware is uploaded to the module (microprocessor) and - after the calibration - electrical and software parameters and protection circuits are being tested. Properly selected test procedures guarantee that every electronics module leaving the production line has the same performance characteristics.
10. EMC Laboratory
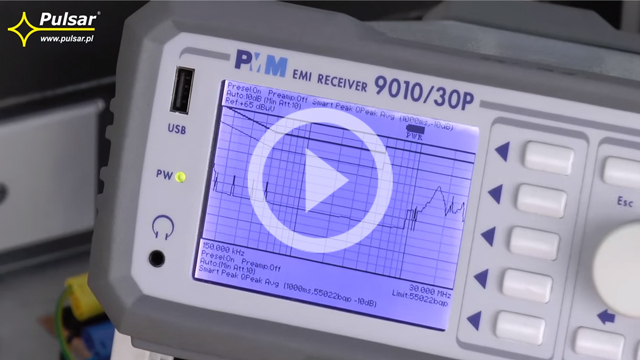
The company owns and operates its own professional EMC laboratory. It allows - at the design stage or after completion of the works - to conduct research in the following areas:
- The measurement of conducted disturbances
- The Measurement of Harmonic Current
- Electrical fast transient/burst immunity test
- Electric and Magnetic Field Coupling to PCB
- and others
The company's ability to carry out immediate tests significantly shortens the process of designing electronic devices.
11. Temperature test chamber
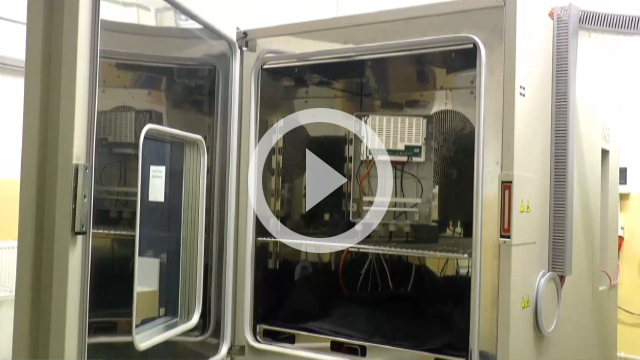
12. obudowy
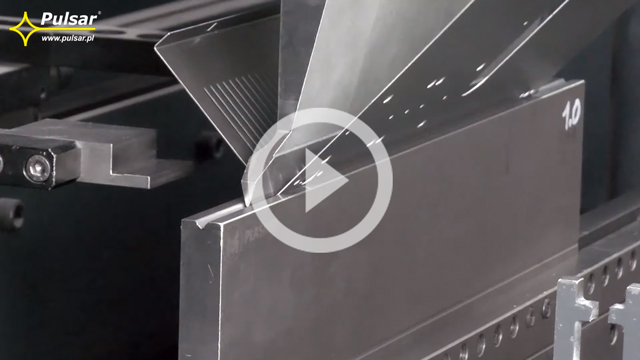
Production of enclosures is based on metal processing, starting from a clean sheet to packaging the final product. The company has the following departments: CNC Punching Department, Press Brake Department, Powder Coating Shop, and other departments supporting the production process. Control at every stage of manufacturing process, including design, cutting, crimping, or powder coating is the breason why all of our products are fully functional and free of defects. More than 20 years of experience and high-quality machinery allow us to meet the expectations of the most demanding customers.
13. Screen printing
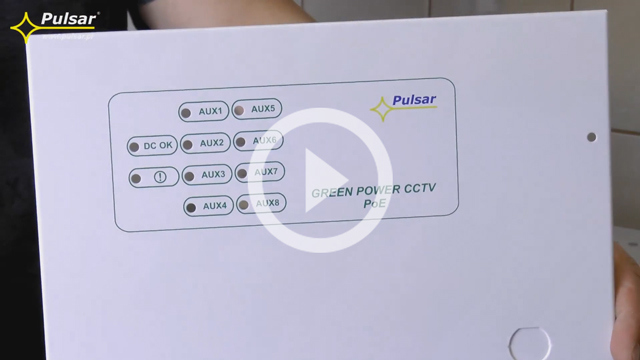
The Pulsar Company offer custom graphics and screen printing on our products. The most commonly used method is screen printing, a printing technique whereby a mesh is used to transfer ink onto a substrate. Screen printing is also a stencil method of print making in which a design is imposed on a screen of polyester which is extremely durable and resistant to scratching.
14. Injection molding machines
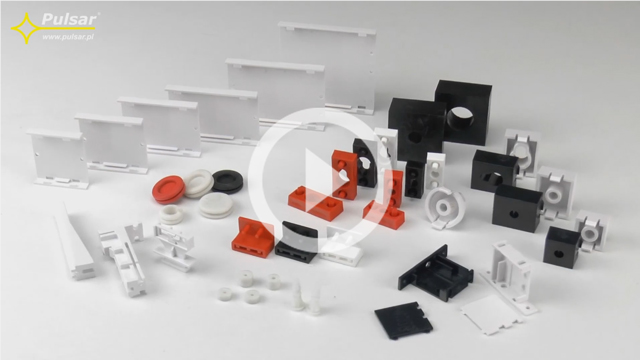
Using injection molding machines by ARBURG, our company produces a whole range of plastics used for the production of electronics and housings. Injection molding machines along with a number of injection molds allows to produce spacers, mounting strips, and transformer enclosures.
15. 3D printer
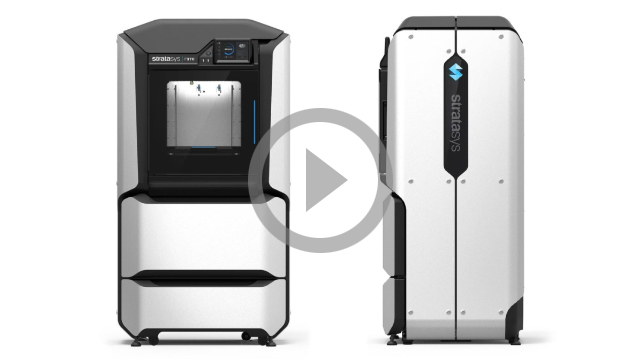
16. Electronics assembly
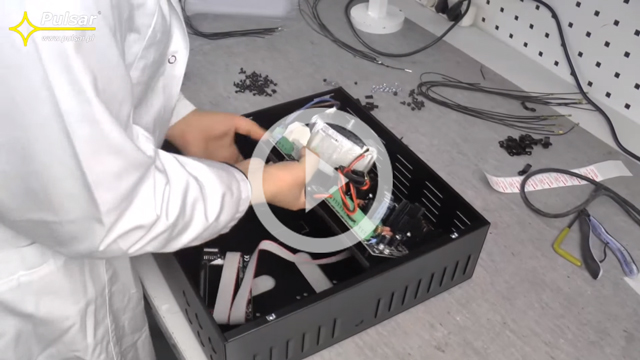
Using injection molding machines by ARBURG, our company produces a whole range of plastics used for the production of electronics and housings. Injection molding machines along with a number of injection molds allows to produce spacers, mounting strips, and transformer enclosures.
17. Storage and Shipping
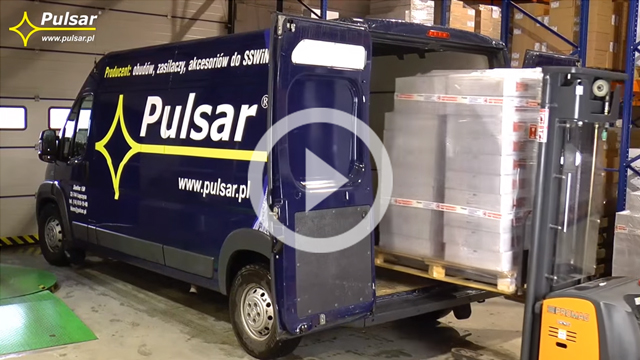
Production area, warehouses, and offices of our company cover an area of over 5000m2. Proper storage and packaging of products allows their adequate protection during transport. The vast majority of shipments is carried out by external professional transport companies. Compliance with the guidelines of the shipping company concerning the preparation of parcels and pallets allows for safe transport to our customers.
Loading...
1. Designing enclosures
2. Punching machines
3. Laser
4. Hydraulic press
5. Robot
6. Electric resistance welding
Arc welding7. Welding machine
8. Semi-automatic spot-welding machine for the production of metal enclosures
9. The production of SMPS connectors
10. Powder coating
11. Semi-automatic powder coating line
12. Screen printing
13. Injection molding machines
14. 3D printer
15. The production of transformers
16. Wire processing
17. Mounting of enclosures
18. Tests
19. Storage and Shipping
1. Designing enclosures
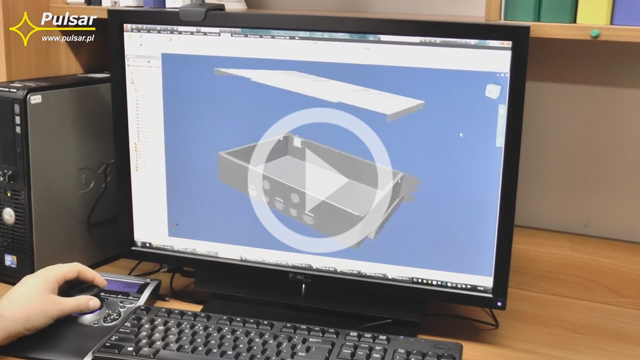
Our engineering staff designs enclosures and housings for power supply units. The advanced software allows precise design of individual housing parts. The prototype is tested and modified several times before the product goes into mass production. We also offer technical advice, custom projects and professional service. We are using the following software:
- Autodesk Inventor - 3D Design
- Autodesk AutoCAD - 2D design - preparation for punching
- 3D PDF Converter - a 3D pdf of the project
In the case of already designed enclosure, we accept the following file types: .dwg, .dxf, .step, .ipt, and .iam.
2. Punching machines
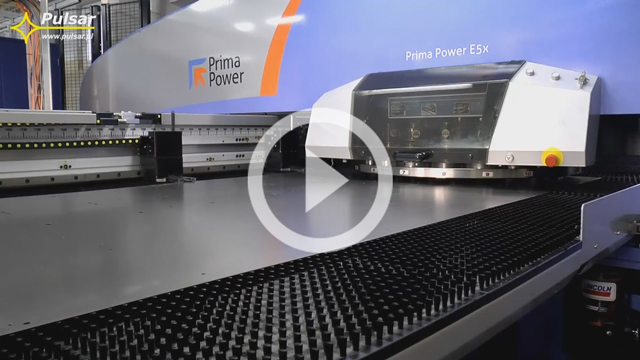
Finished enclosure projects are punched by CNC punching machines. These are cutting down the desired forms from metal sheets. Punching machines automatically move sheets, punching various kinds of holes, including: rectangle, circle, ellipse, and others - depending on the needs. The device also allows to punch pre-embossed openings by simultaneously cutting the desired shape and and embossing the sheet. In addition, there is the possibility of stamping serial numbers / names / symbols / logos on a given part of the enclosure. The use of CNC punching machines ensiures precise cutting and repeatability of elements.
3. Laser
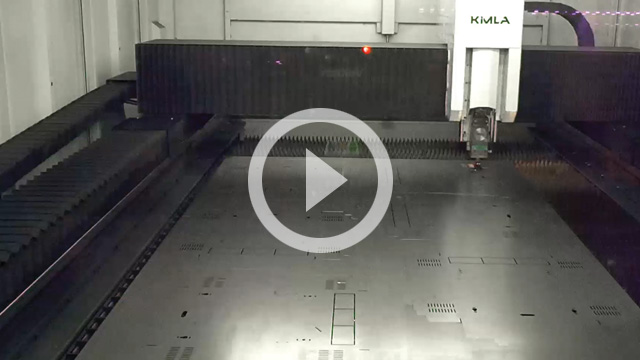
4. Hydraulic press
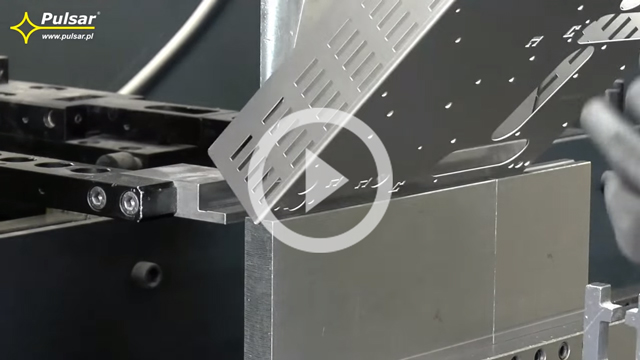
The high quality and repeatability of our products is guaratnteed by the use of professional press brakes by SAFAN DARLEY. Their accuracy allows us to faithfully reproduce the project in the actual product. Their versatility allows the processing of sheets with a thickness of 0.5 ÷ 3 mm and lengths of up to 1.6 m. Simple operation allows to obtain high quality and repeatability of each designed element.
5. Robot
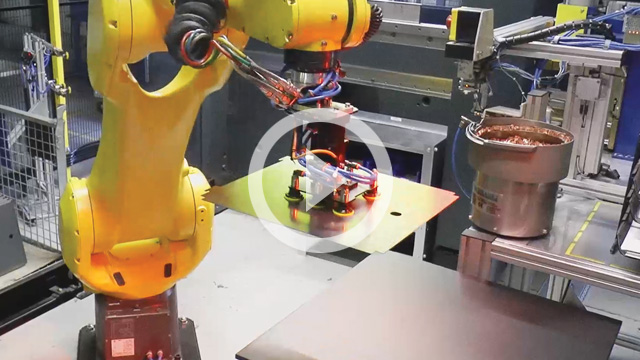
6. Electric resistance welding
Arc welding
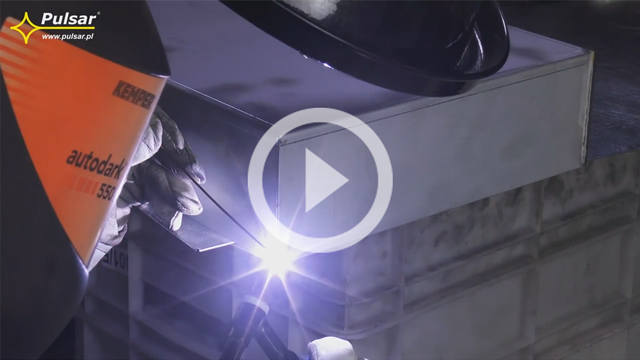
Depending on the enclosure type and its operation conditions, different processes for welding and joining materials are being used. Welding and fusion welding are the most commonly used metods in our company. In the first case,work pieces are welded due to a combination of a pressure applied to them and a localized heat generated by a high electric current flowing through the contact area of the weld. When the current is stopped, the molten metal solidifies under pressure. Meanwhile, Arc welding is a type of welding that uses a welding power supply to create an electric arc between an electrode and the base material to melt the metals at the welding point. The vast majority of enclosures is produced with use of Electric resistance welding due to lower costs and time involved.
7. Welding machine
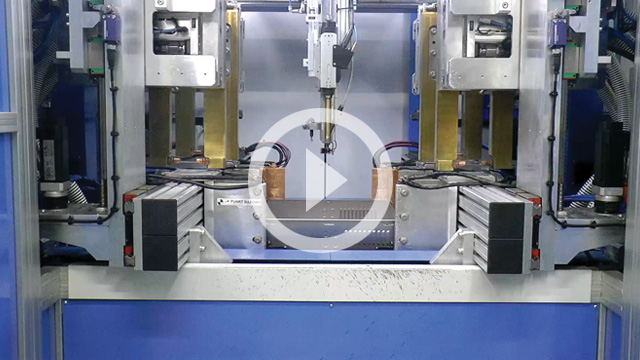
8. Semi-automatic spot-welding machine for the production of metal enclosures
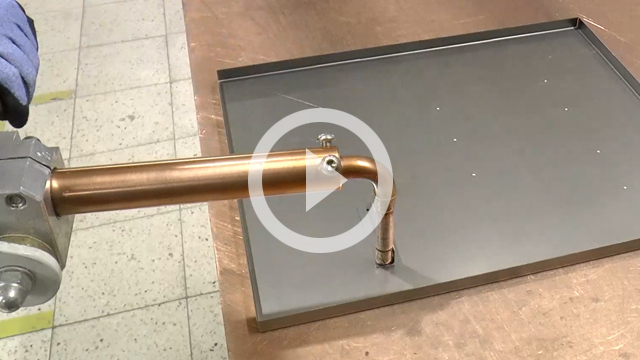
We use semi-automatic spot-welding machines for the production of metal enclosures at Pulsar. The welding process takes place by concentrating heat and pressure in a small area. The first electrode is placed on the worktable, the second is, spot electrode, placed on a movable arm. As a result of the point pressure and the flow of an appropriately selected current, two sheets of metal are permanently connected together. This method has many advantages, including that it can be used to weld different types of metals and their thicknesses. The presented welding machine is one of several used in Pulsar's production lines. The selection of the appropriate one is related to the design of the enclosure to be made.
9. The production of SMPS connectors
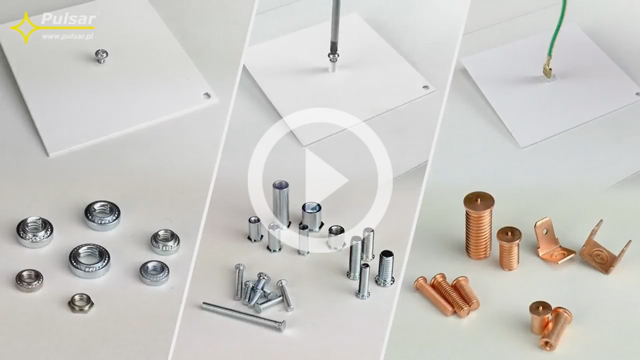
We have dedicated equipment for the connection of small threaded pins, bushings or connectors. Bushings mounted in metal are automatically administered into the device and pressed with adequate pressure. In the case of grounding connectors, they are welded to steel sheets. These connections are durable and aesthetic, can be used to mount the PCB elecctronic modules in enclosures, for detachable connections of two steel elements or for grounding of housings or power supply units.
10. Powder coating
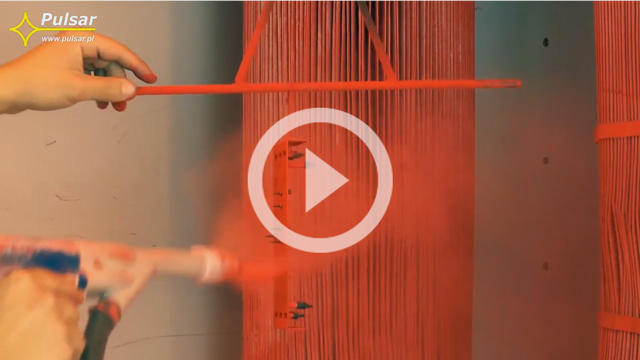
Before powder coating, the enclosures undergo a series of processes for the proper preparation of the surface. These include, among others, cleaning and protecting the surface with use of dedicated chemical solutions in ultrasonic baths. The next step is the protection of connectors and grounding terminals against painting. The painting process is performed in special ventilated booths using dedicated equipment suitable for powder coating. The final step is curing in an appropriate oven resulting in a durable and aesthetic coating. Several housings from each production batch are checked for the quality of the painted surface and paint thickness.
11. Semi-automatic powder coating line
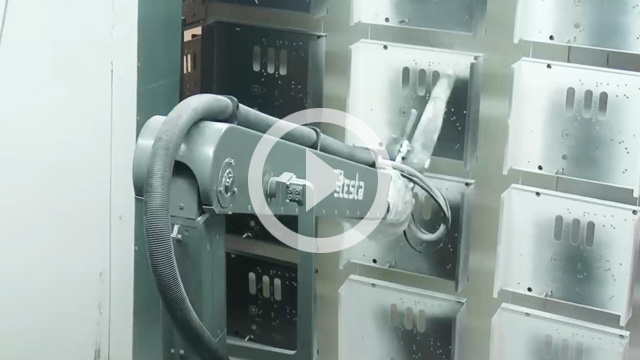
Enclosure painting process at Pulsar takes place semi-automatically. The enclosures with properly prepared surface (free of dirt, dry and chemically protected against corrosion) are placed on a line in constant motion. Painting is performed automatically by moving arms of an industrial robot armed with a spray gun. The electrostatically charged powder reach successfully also the most inaccessible areas of the surface to be painted. The enclosures with applied powder are placed in an automatic tunnel oven, where after an appropriate heat treatment time, the surface acquires the appropriate properties, including colour or mechanical properties, depending on used paint. Powder coating is a popular finishing method for metal enclosures due to its durability and effectiveness.
12. Screen printing
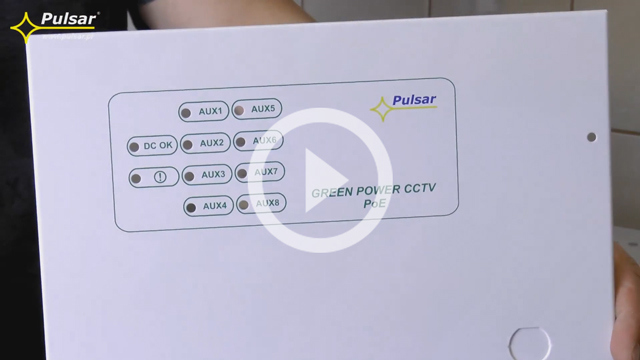
The Pulsar Company offer custom graphics and screen printing on our products. The most commonly used method is screen printing, a printing technique whereby a mesh is used to transfer ink onto a substrate. Screen printing is also a stencil method of print making in which a design is imposed on a screen of polyester which is extremely durable and resistant to scratching.
13. Injection molding machines
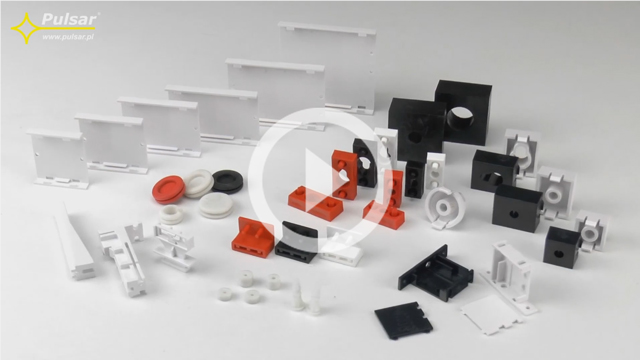
Using injection molding machines by ARBURG, our company produces a whole range of plastics used for the production of electronics and housings. Injection molding machines along with a number of injection molds allows to produce spacers, mounting strips, and transformer enclosures.
14. 3D printer
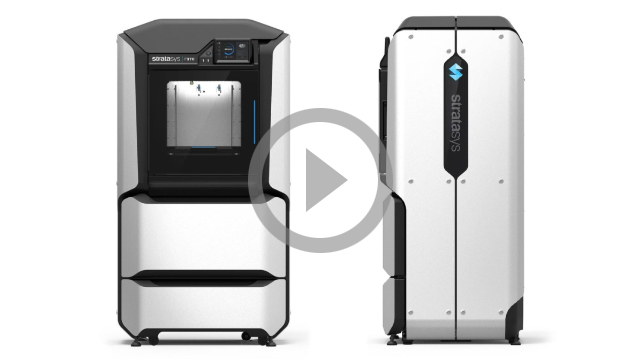
15. The production of transformers
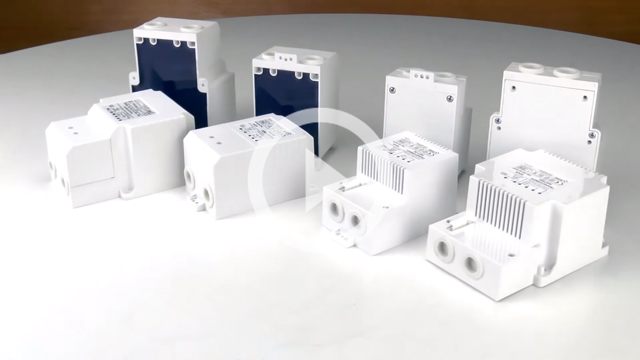
Our company offers transformers of the following series: T (IP43), TRP (IP30), TOR, and EI with power ranging from 20 VA to 300 VA. Transformer enclosures (TRZ, TRP) are made of PC/ABS, UL 94 V-0 class. Transformers of the TRZ series, cast epoxy resin, IP43 protection class. In the final stage of the production process, transformers undergo a number of tests. These include, among others, high-voltage AC dielectric test and DC insulation resistance measurement using the certified MI 2094 CE Multitester by METREL.
16. Wire processing
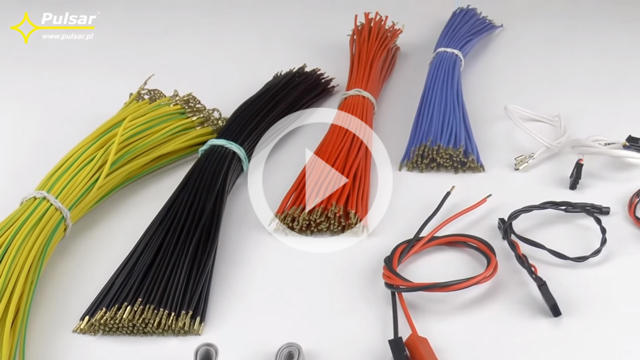
The Gamma 263 S crimping machine by KOMAX enables fully automatic wire processing. The device precisely cuts wires to a desired length and allows one and two-sided crimping. The maximum cross-section of the processed cable is up to 4mm2 with cable lengths from 4 cm to 20 m. Full control of the quality of the crimped connector is ensured by the certified Universal Tester Model CT 50 by MAV PRÜFTECHNIK for tensile strength measurements. Indication range: 0-500 N.
17. Mounting of enclosures
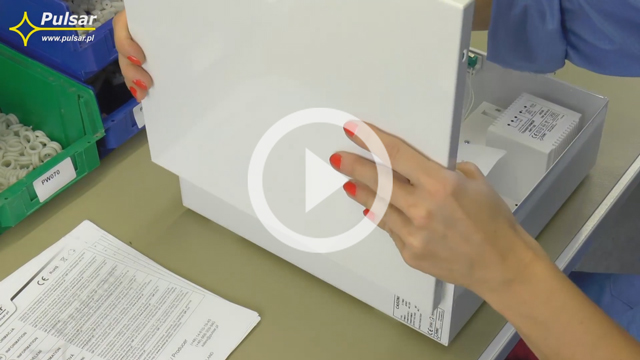
The last stage of the production process of enclosures is the assembly line. At this stage, the product is finally assembled, tested and packaged. The ISO 9001:2008 quality management certificate is a guarantee that our customers receive fully functional and high quality products.
18. Tests
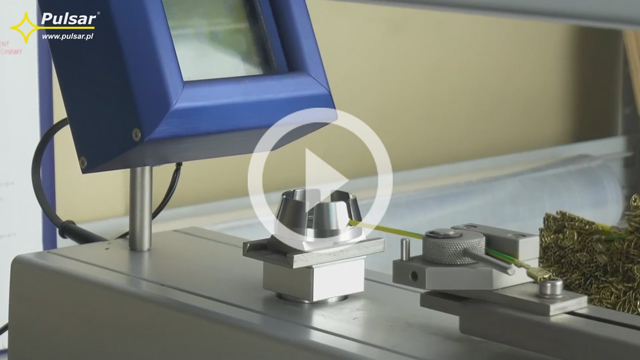
Metal sheet parameters, the weld strength, the thickness of paint coating, the grounding, and connector clamps are checked at every stage of the production of metal enclosures. The implementation of this type of control at each stage of the production process allows us to offer a 100% Customer Satisfaction Guarantee.
19. Storage and Shipping
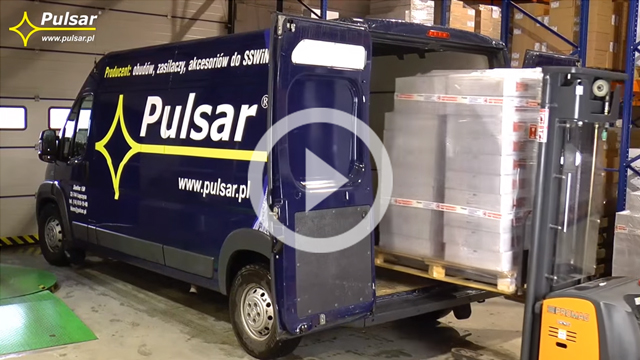
Production area, warehouses, and offices of our company cover an area of over 5000m2. Proper storage and packaging of products allows their adequate protection during transport. The vast majority of shipments is carried out by external professional transport companies. Compliance with the guidelines of the shipping company concerning the preparation of parcels and pallets allows for safe transport to our customers.
If you're interested, please contact our sales department
Contact us